Custom 3D Printer Builds
Building and tuning various 3D printers from the ground up, including CoreXY and other designs, to achieve specific performance and quality goals.
My deep dive into 3D printing began during its early consumer days, when the machines were full of potential but far from perfect. To truly grasp the technology, I took a hands-on approach, systematically modifying a wide variety of printers. This process allowed me to deconstruct and understand the fundamental design principles behind critical systems: the intricacies of hotend and extruder design, the trade-offs between different motion platform mechanicals, and the complexities of the firmware controlling it all. Each modification presented a unique challenge, and by tackling them directly, I built a deep, holistic understanding of 3D printer engineering from the ground up.
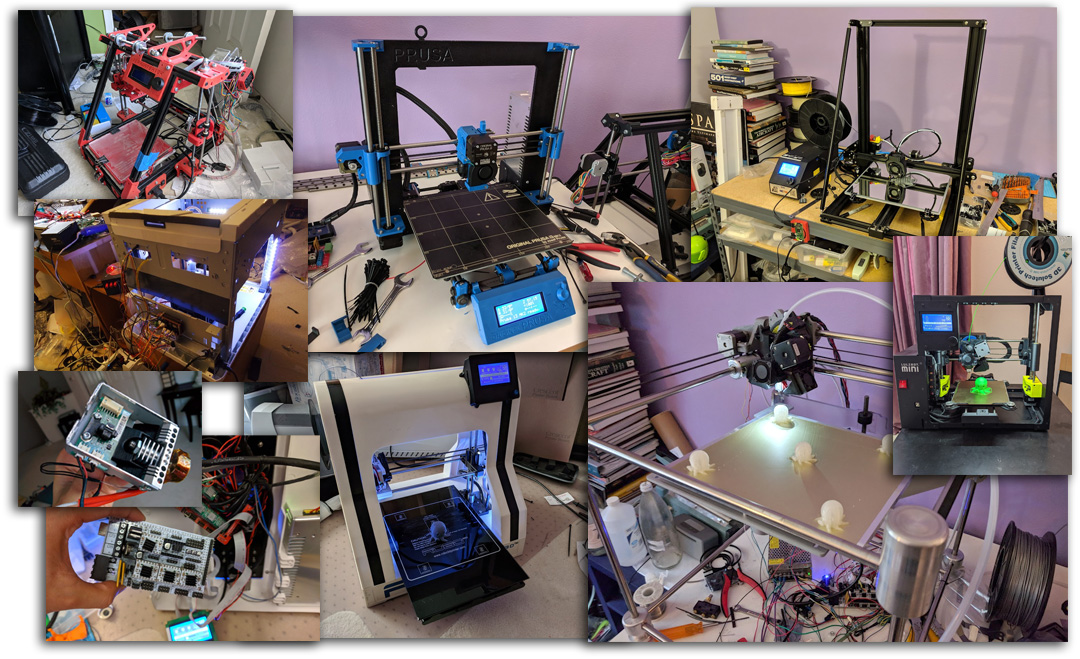
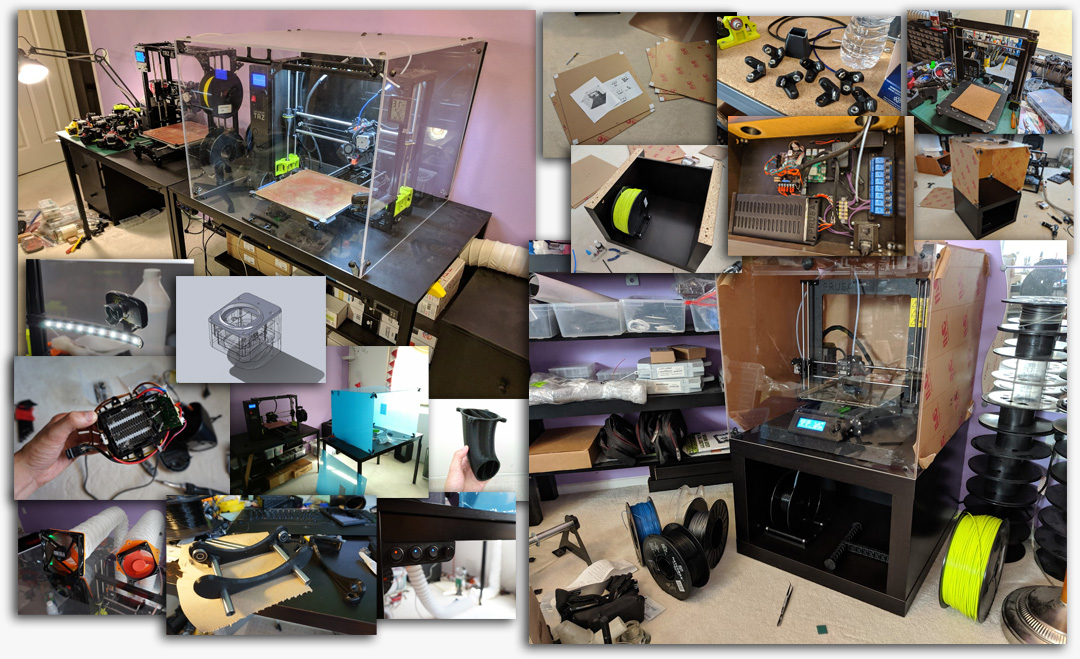
While modifying existing printers is a great way to improve performance, I've always believed that the deepest understanding comes from building a machine from its core components. Around that time the CoreXY motion system was gaining popularity, so I therefore incorporated it into my early stages of researching and designing my own 3D printer from the ground up. After posting my early designs in multiple 3D printing communities, I learned through feedback that my work shared many similarities with a relatively new and unknown project at the time, Voron. I then joined the community of Voron builders and made several contributions to the design that helped it become what it is today. This section showcases my journey into developing and building my custom Voron 3D printer.
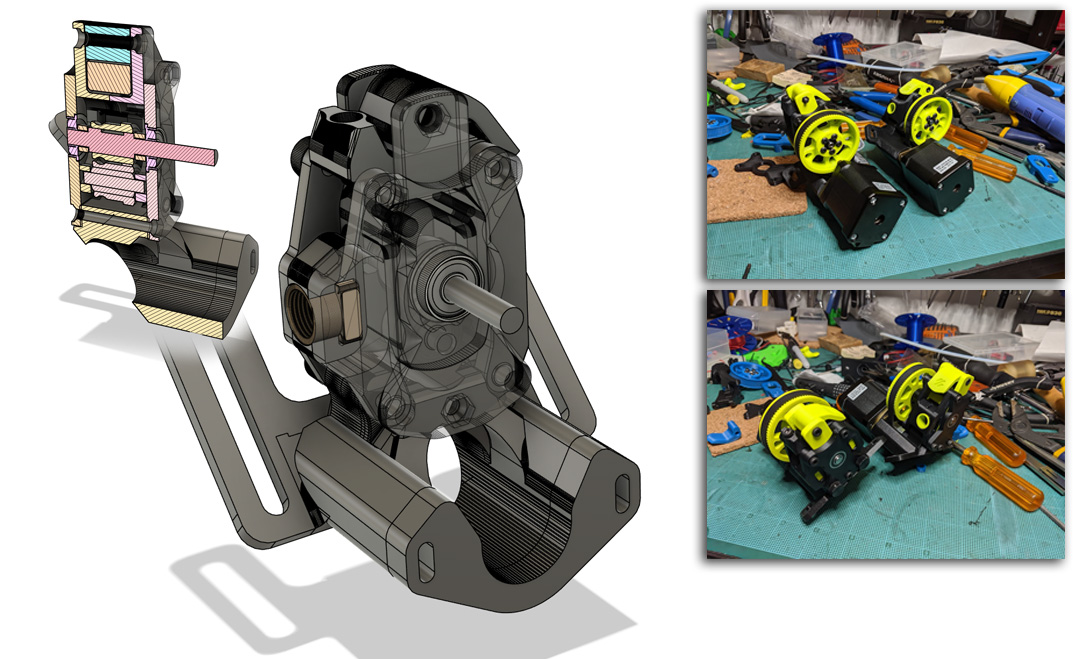
Aiming for ultimate flexibility with this Voron build, I set out to solve the issue of varying filament standards from the start. Possessing a large stockpile of 2.85mm filament but wanting access to the wider 1.75mm market, I incorporated a dual-extrusion concept directly into the initial design phase. This involved a complete re-engineering of the standard extruder into a symmetrical, two-sided system that shared key components, effectively giving my Voron the ability to print with any filament I had on hand.
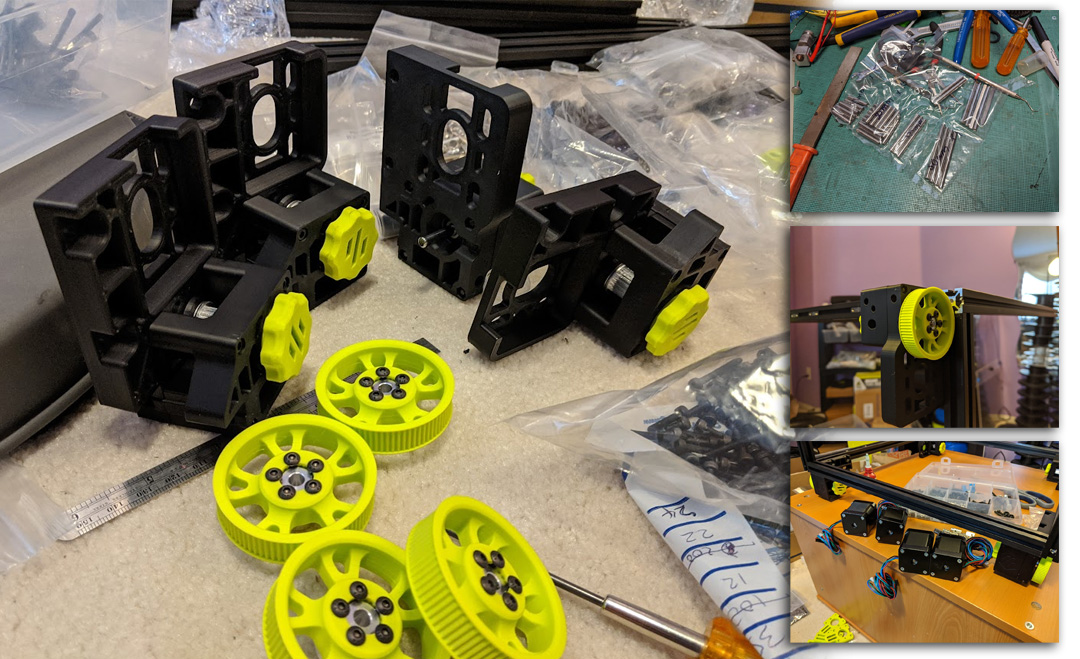
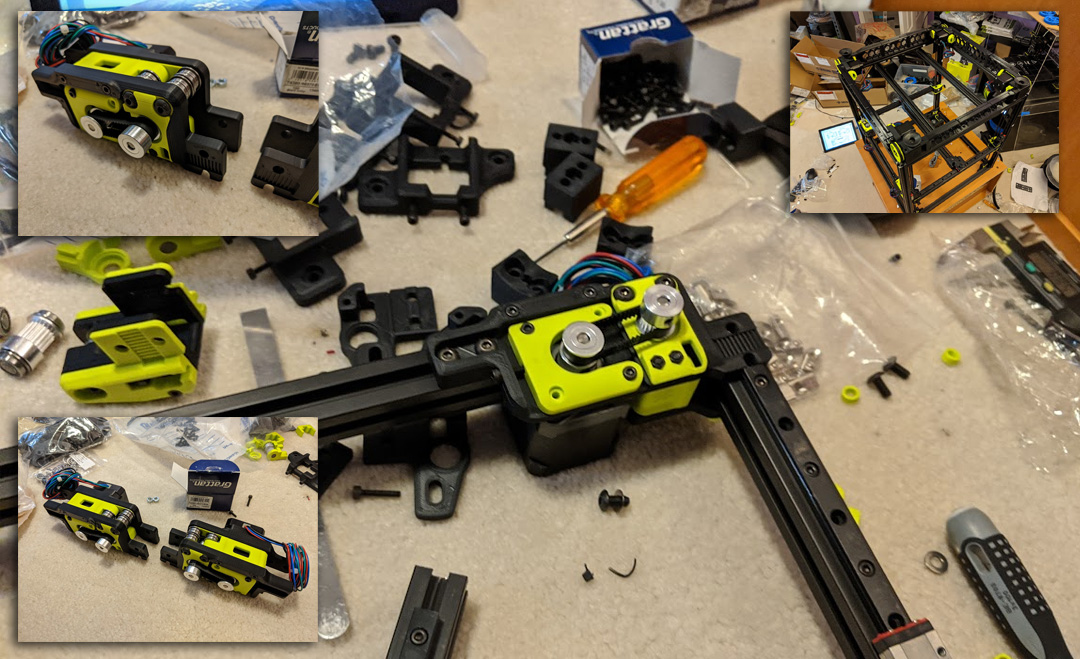
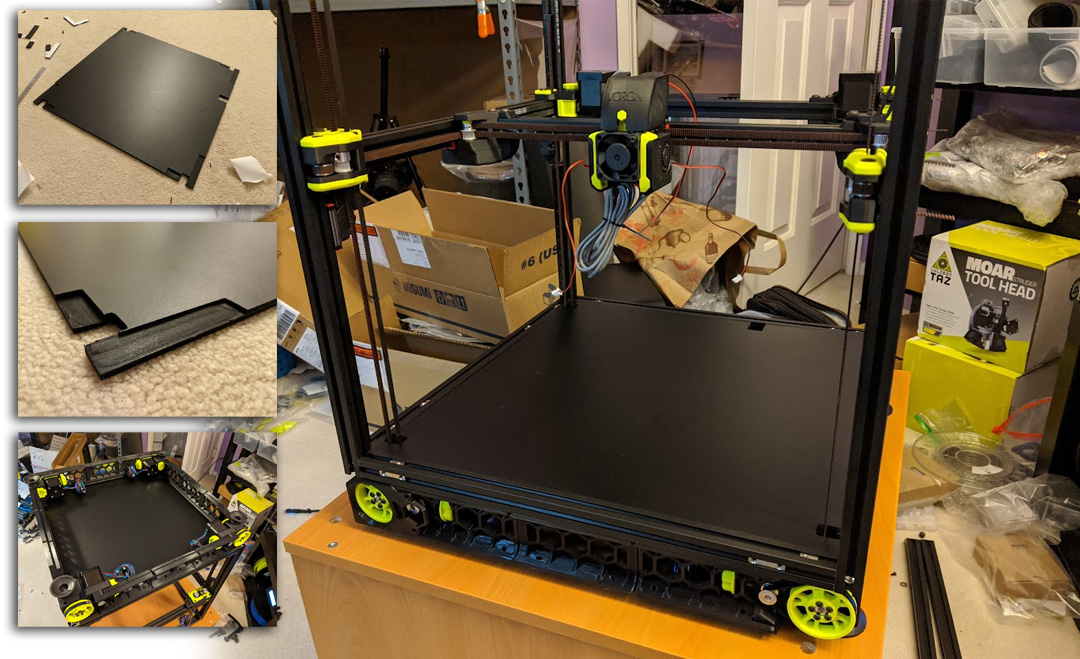
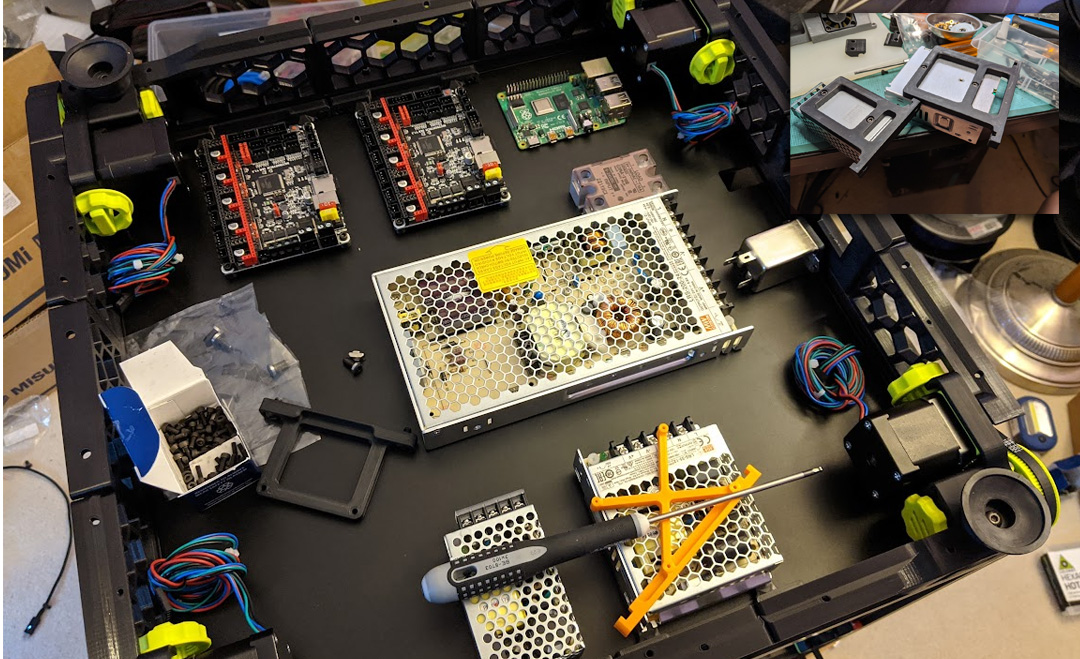
For the electronics, I opted for a completely custom component mounting solution to achieve total control over the system's layout and wiring paths. This level of customization was essential to neatly accommodate the complex array of hardware: multiple controller boards, several independent power supplies, and a relay controller board for software-based control of various accessories. A key feature of this design was the integration of a custom quick-disconnect wiring harness, which greatly simplifies any future maintenance or system modifications.
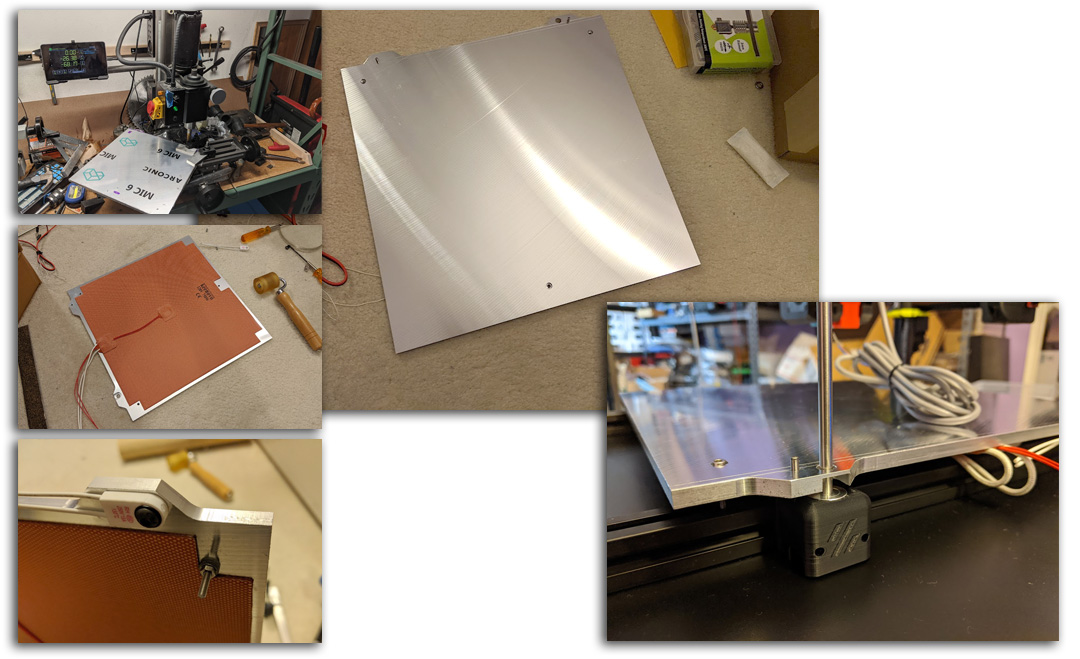
The pursuit of precision extended to every component, including a fully customized build plate. I machined it from a 1/8" MIC6 precision cast aluminum tooling plate, specifically chosen for its exceptional thermal stability and flatness. To manage thermal expansion, I implemented a 3-point kinematic mounting system with built-in compliance. For workflow efficiency and perfect first layers, I integrated alignment pins that ensure the magnetic flex plate is always highly repeatable and accurate in its positioning. As a final touch, a through-plate Z-endstop was incorporated into the design, a purely aesthetic choice for a cleaner, more integrated look.
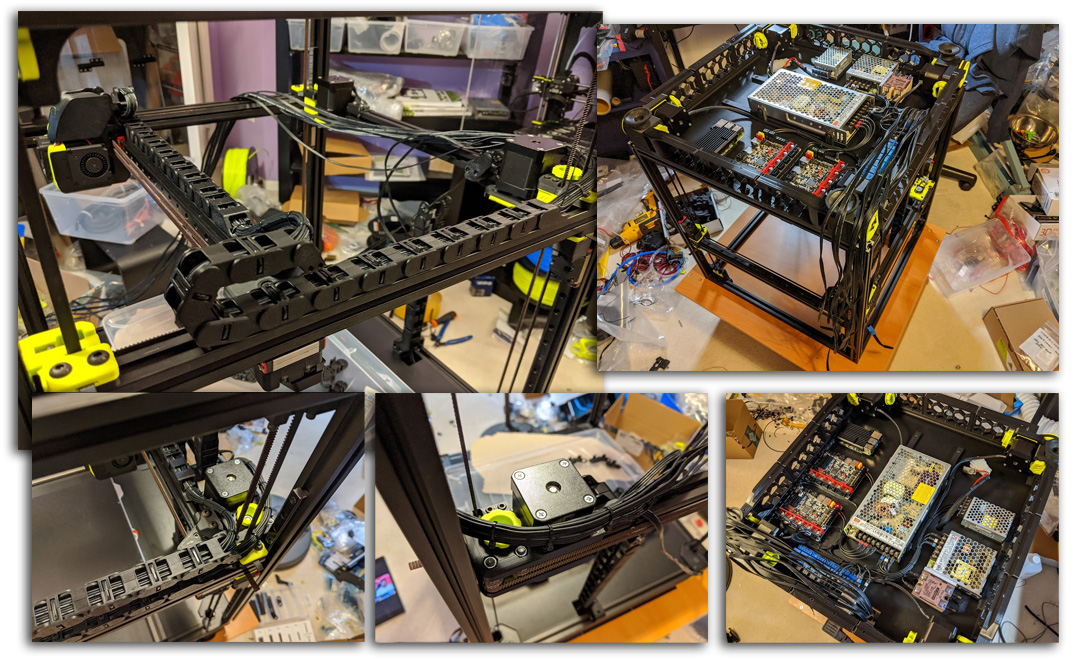
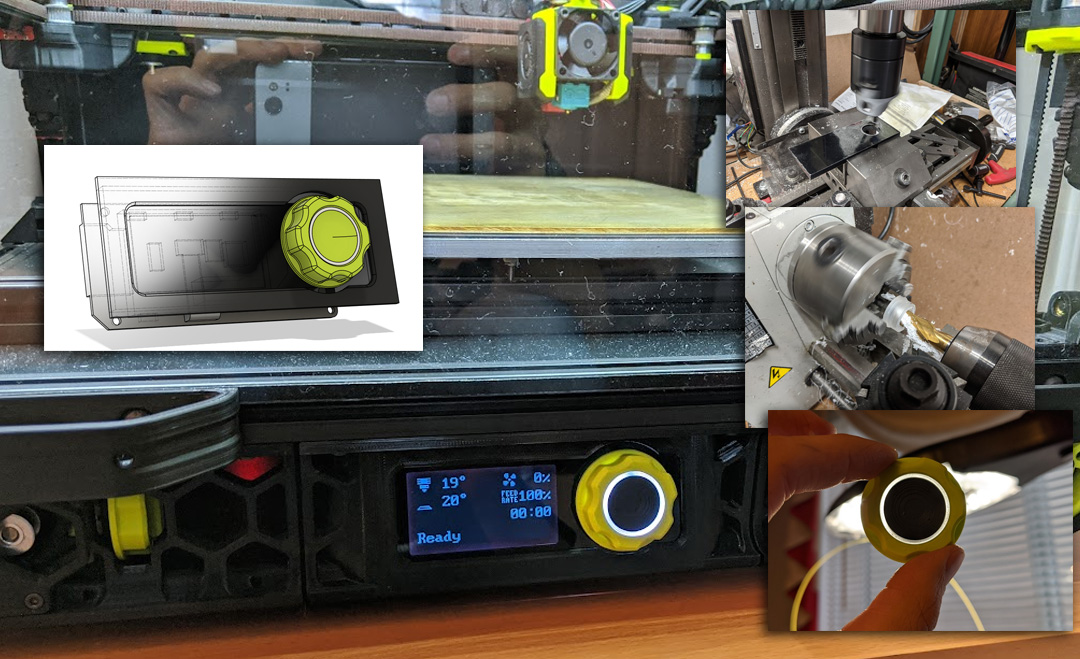
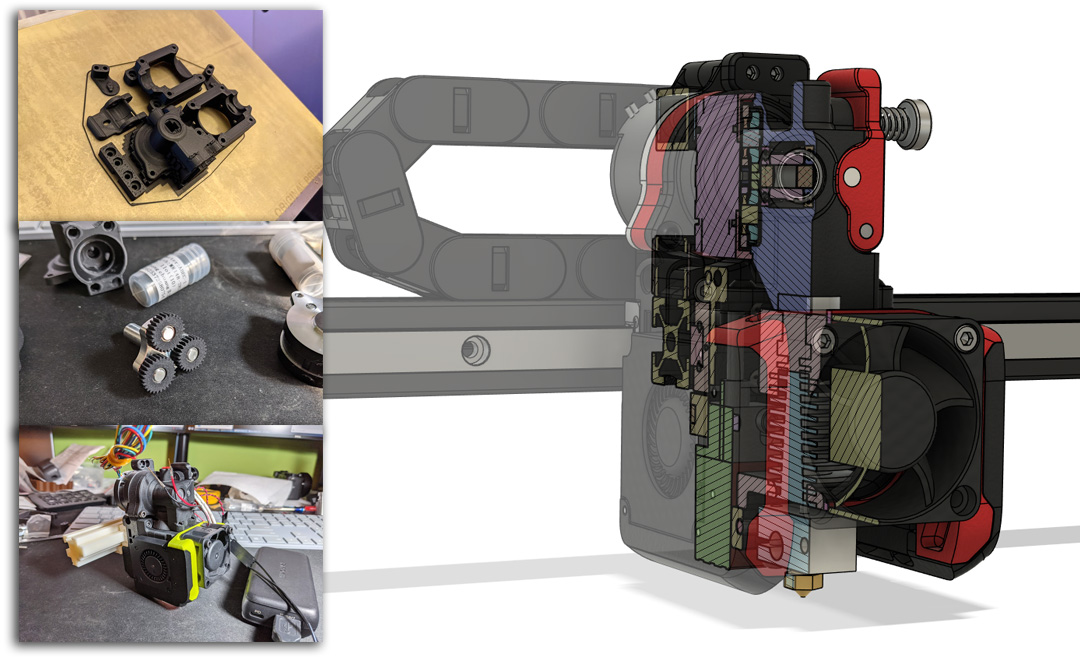
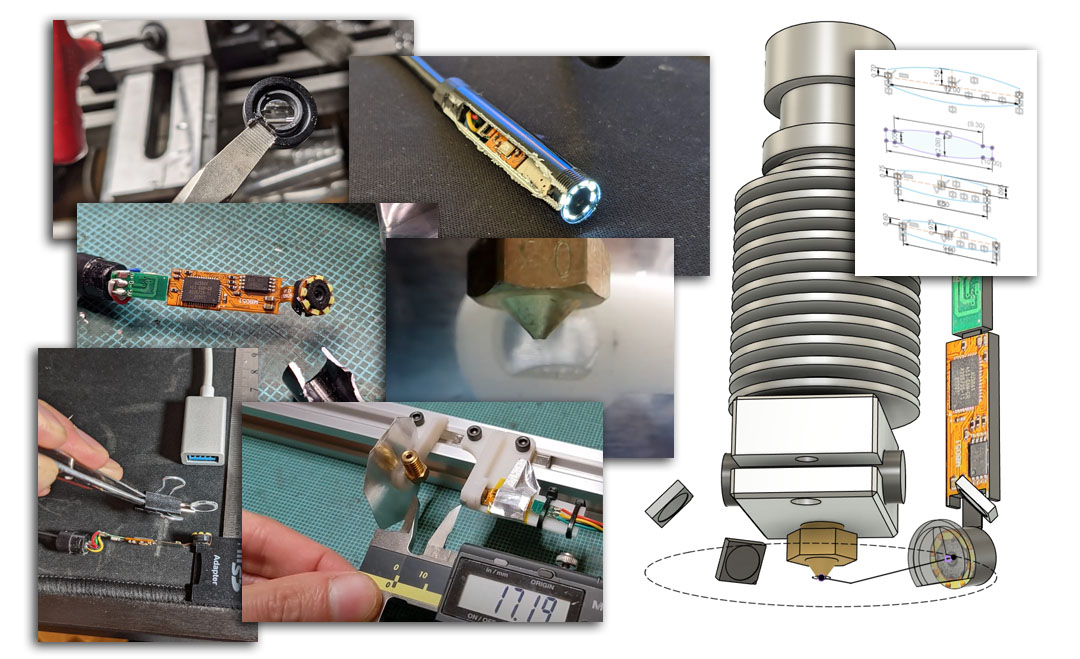
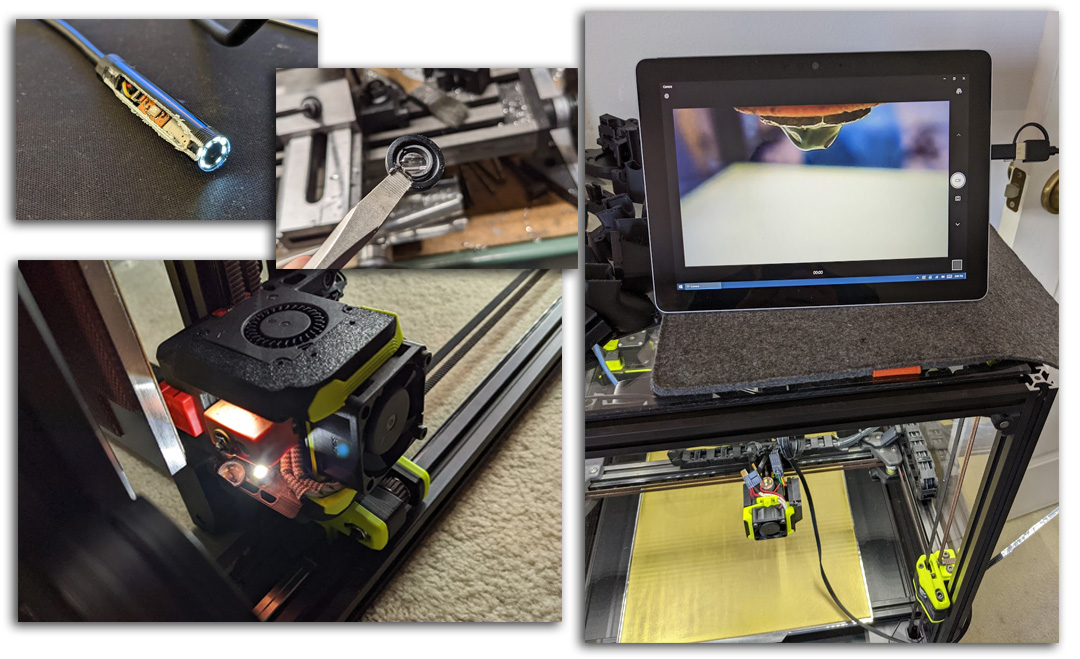
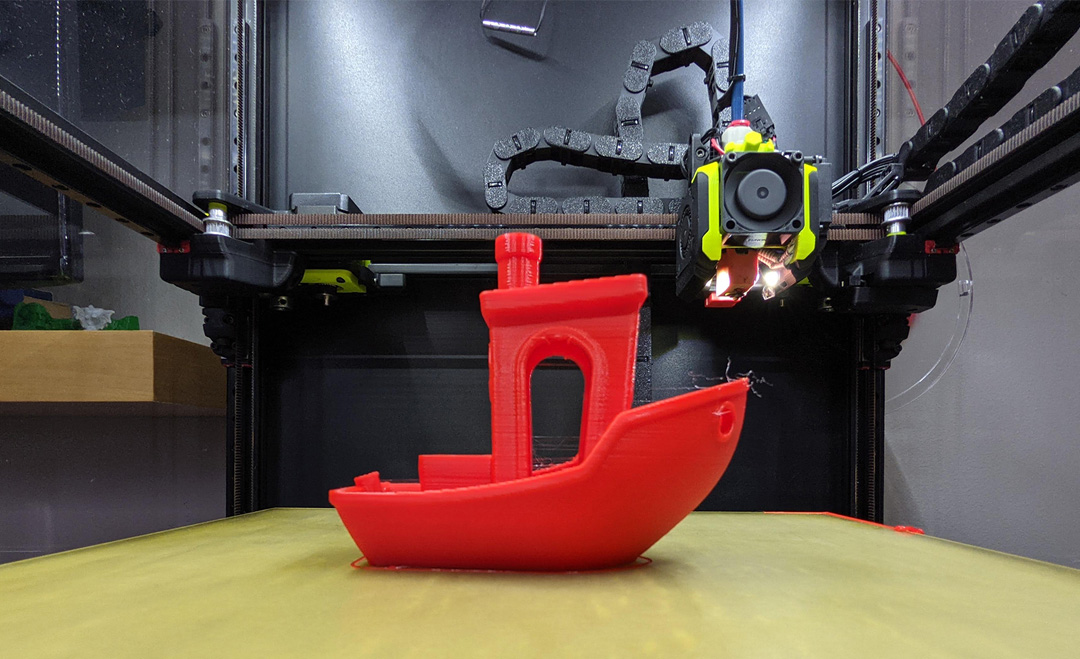
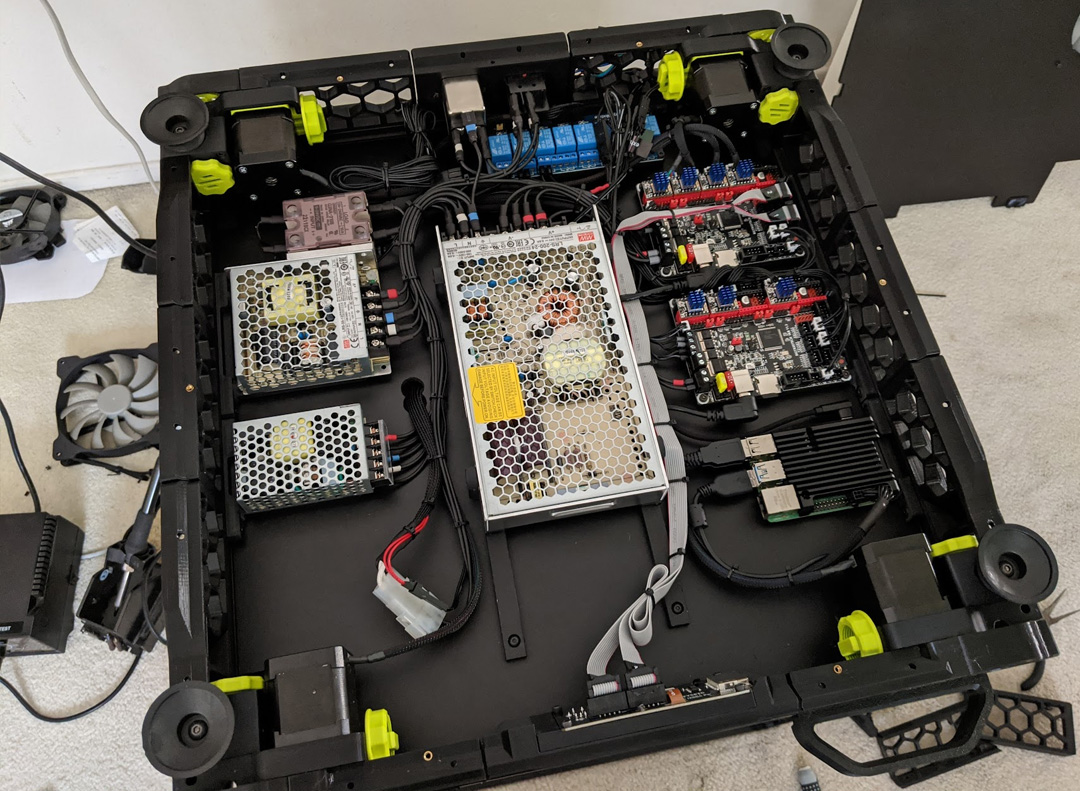
Building this printer from its core components was an invaluable lesson in how to design for functionality, reliability, and performance. The process provided a deep, hands-on understanding of how mechanical systems, electronics, and software must work in perfect concert to create a truly cutting-edge machine.