Advanced Fabrication:
Composites & Automotive Paint
Detailing projects that involve designing and creating custom car parts from composite materials and applying professional-grade painting and finishing techniques.
My passion for cars and fabrication extends to the challenge of creating parts that are both lightweight, strong, and aesthetically perfect. This led me to explore composite materials like carbon fiber and fiberglass, which offer incredible design freedom. This section of my portfolio details various projects where I've designed and fabricated custom automotive parts using techniques such as free hand sheet metal shaping, wet layup, and vacuum bagging, followed by a meticulous, multi-stage process of automotive painting to achieve a professional, show-car-quality finish.
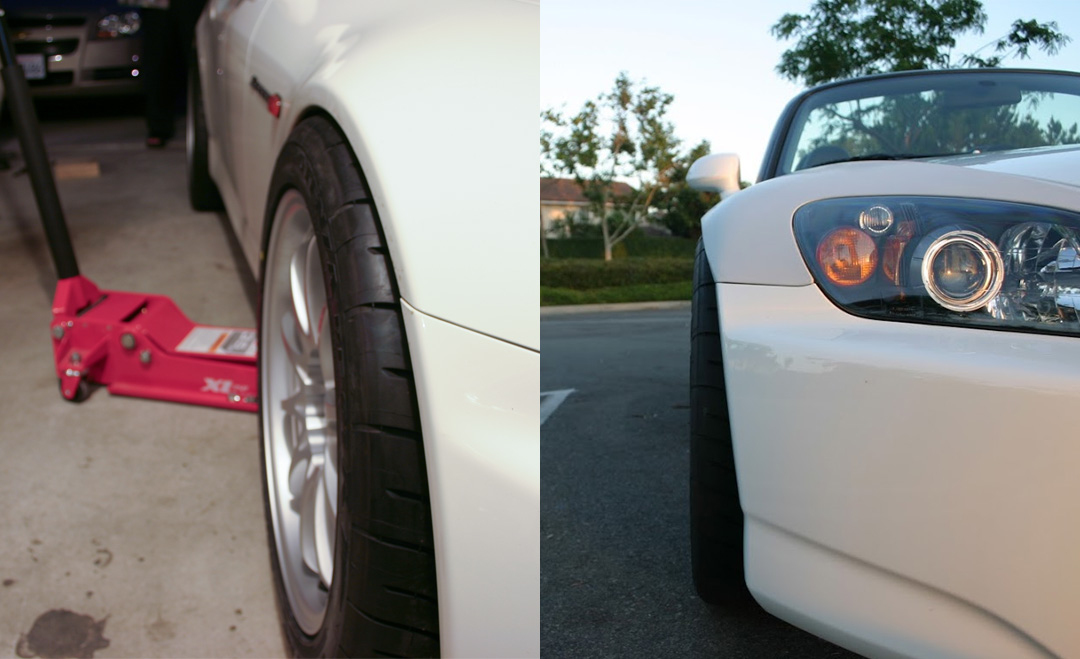
The goal of this project was to widen the factory steel fenders by approximately one inch to accommodate wider tires for improved track performance. Starting with a pair of damaged OEM fenders, I first repaired the existing imperfections. The first step of this project was the intricate metalwork before making a mold to create composite copies: I hand-hammered the arches outwards, deliberately removing the factory body line along the opening to create a new, wider profile. The final step in the metal shaping was to form a clean transition triangle, ensuring the new, wider fender flowed seamlessly into the lines of the front bumper.
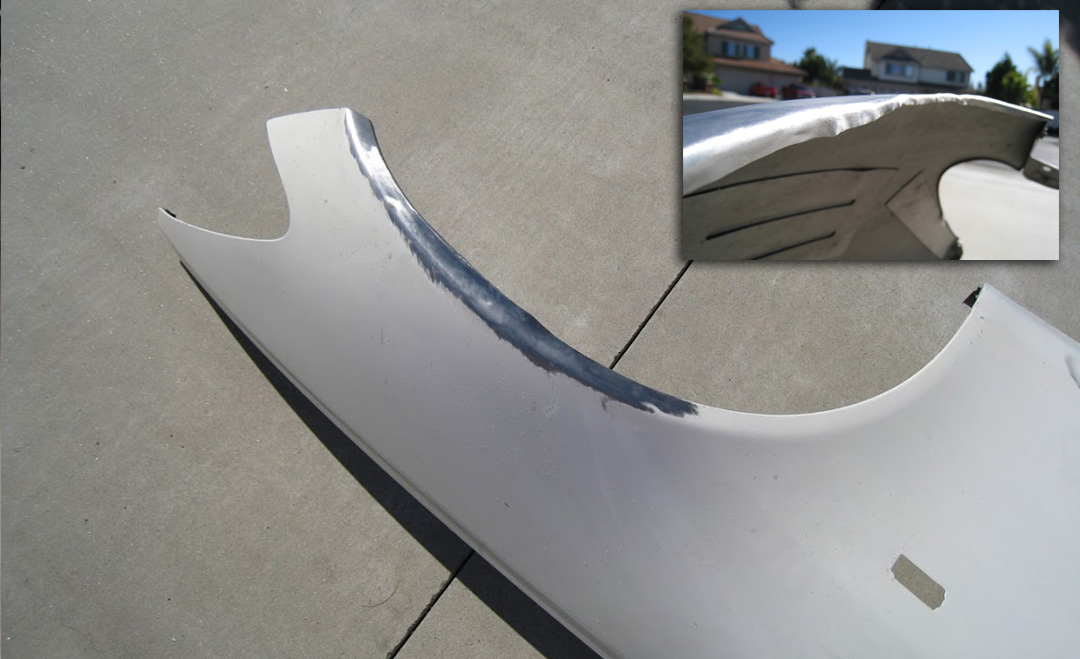
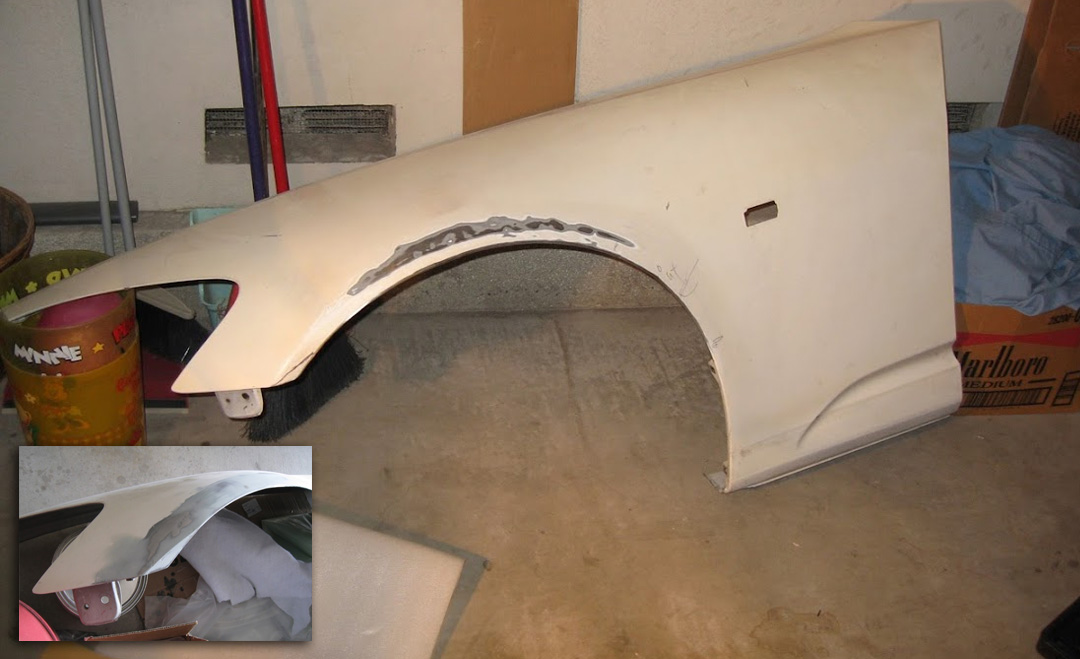
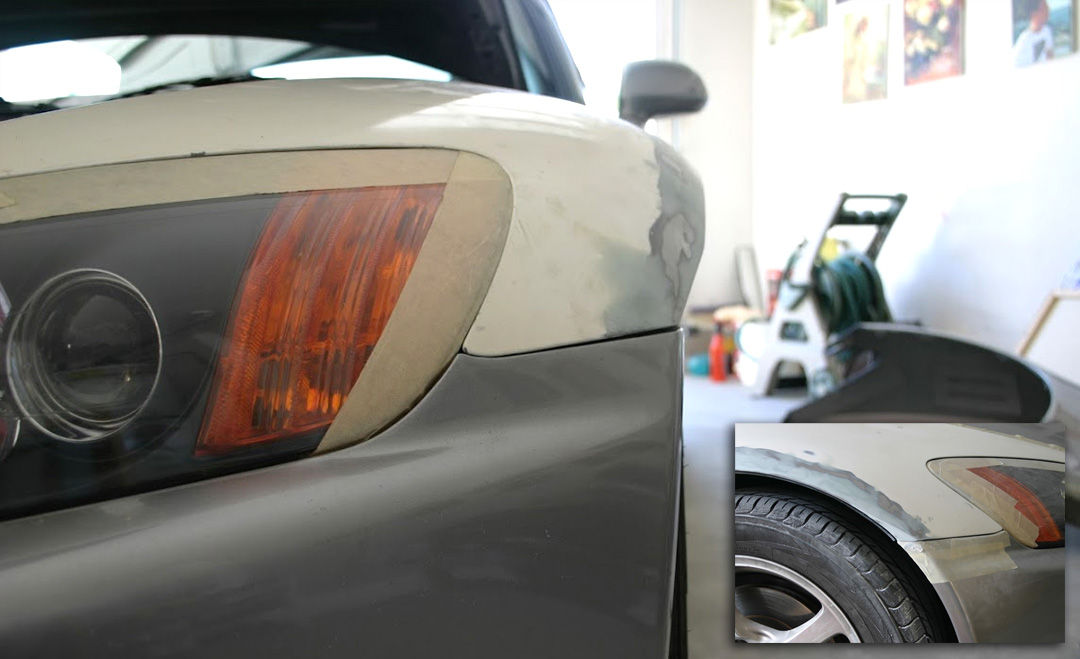
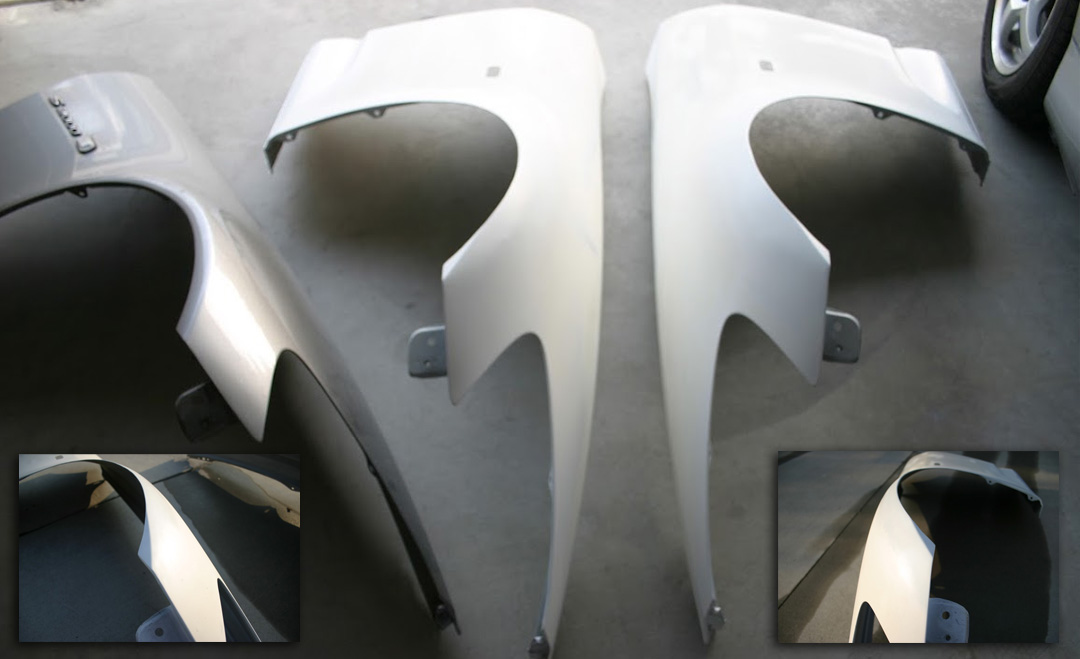
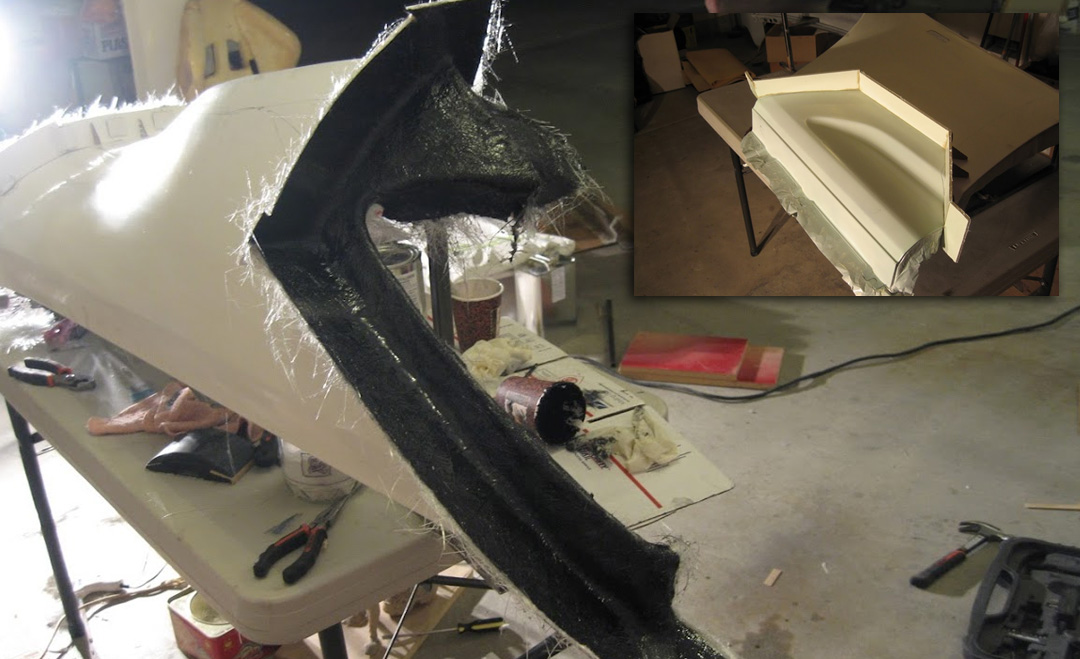
Once the metalwork was complete, the reshaped fender's surface was carefully prepped and smoothed to serve as the master plug for the mold. I constructed flanges for a multi-part mold using foam core board, with the seams carefully sealed with clay to ensure a clean parting line. To guarantee a perfect release, the surface was first waxed multiple times and then coated with a PVA (Polyvinyl Alcohol) release agent. The mold creation began with a layer of gel-coat to capture the fine surface details, followed by laminating appropriate layers of chopped strand mat fiberglass, which were thoroughly wetted out with resin to build a strong and durable mold.
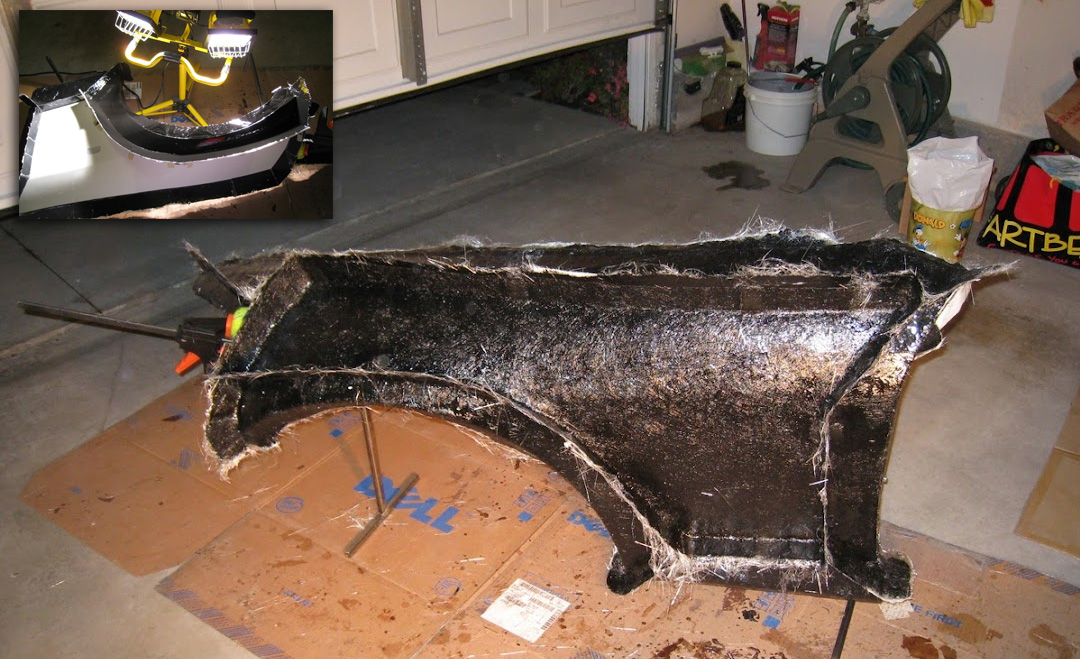
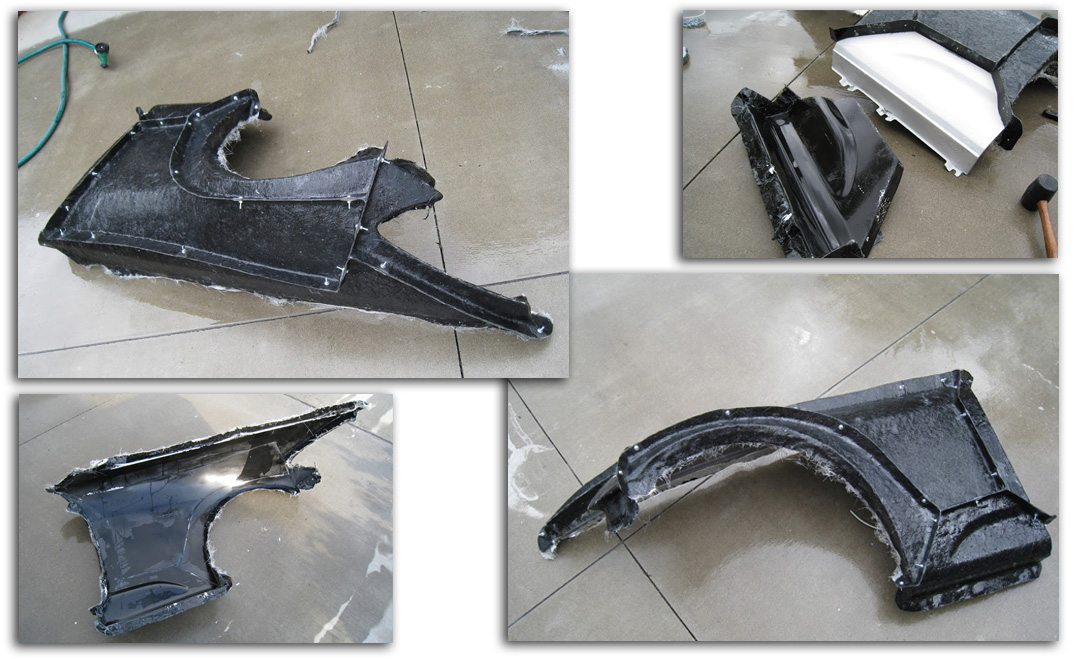
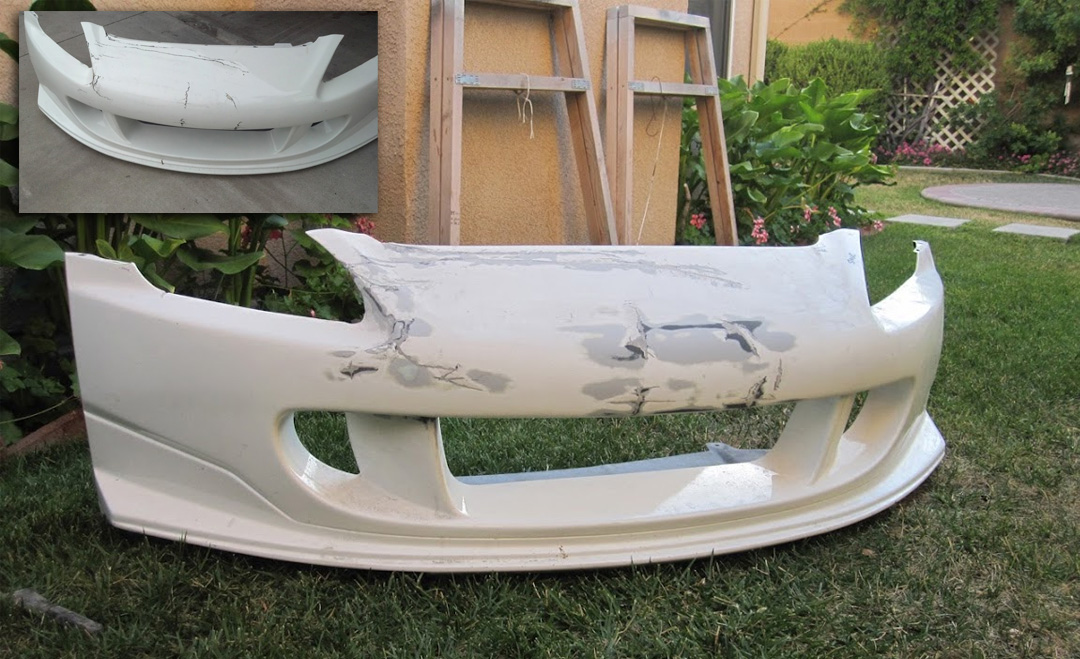
My composite fabrication skills are showcased in this repair project, which involved both repairing and recreating a fiberglass front bumper. The process started with extensive repairs to a damaged bumper to bring it to a flawless state. Using similar fiberglass techniques, I then made a negative multi-part mold from the restored bumper. The final stage was to use this new mold to lay up and produce a brand new, structurally sound fiberglass bumper, completing the journey from a damaged original to a perfect copy.
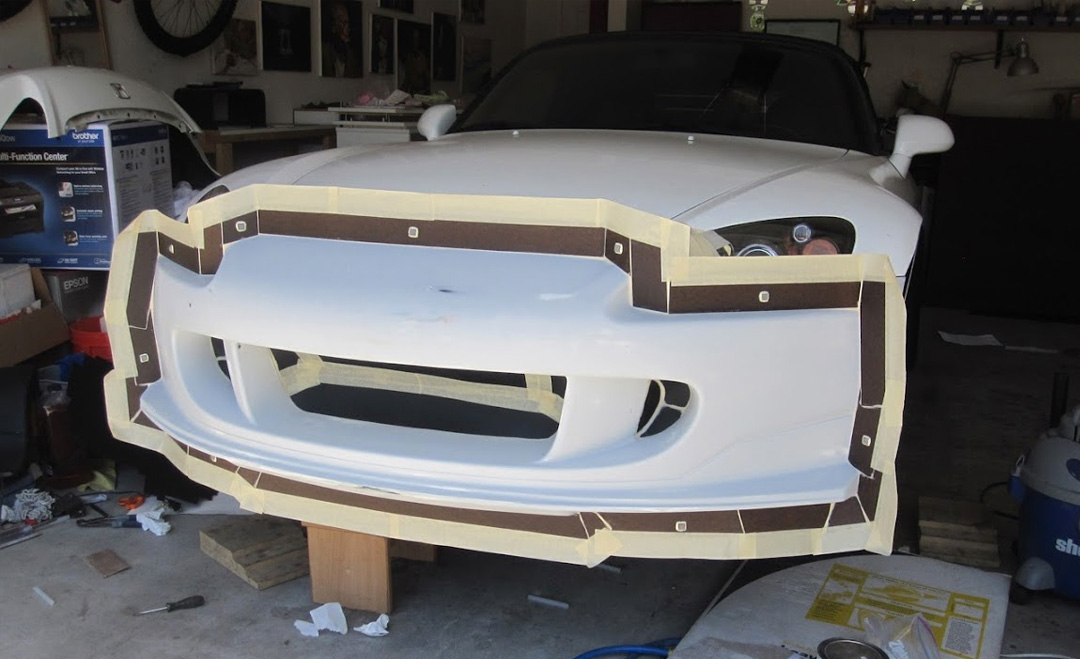
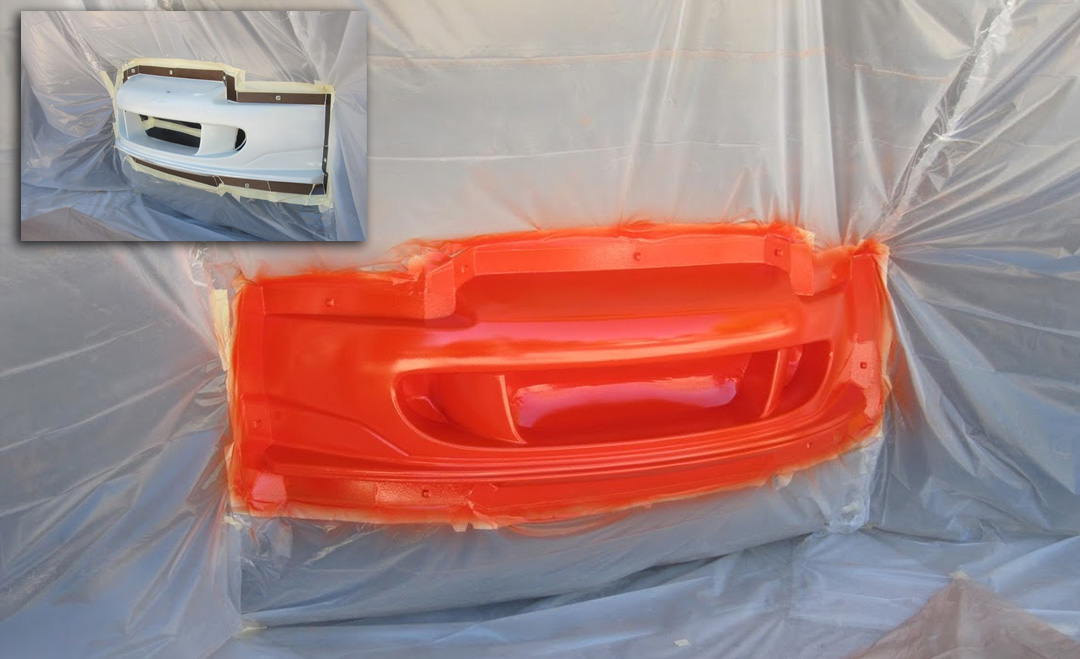
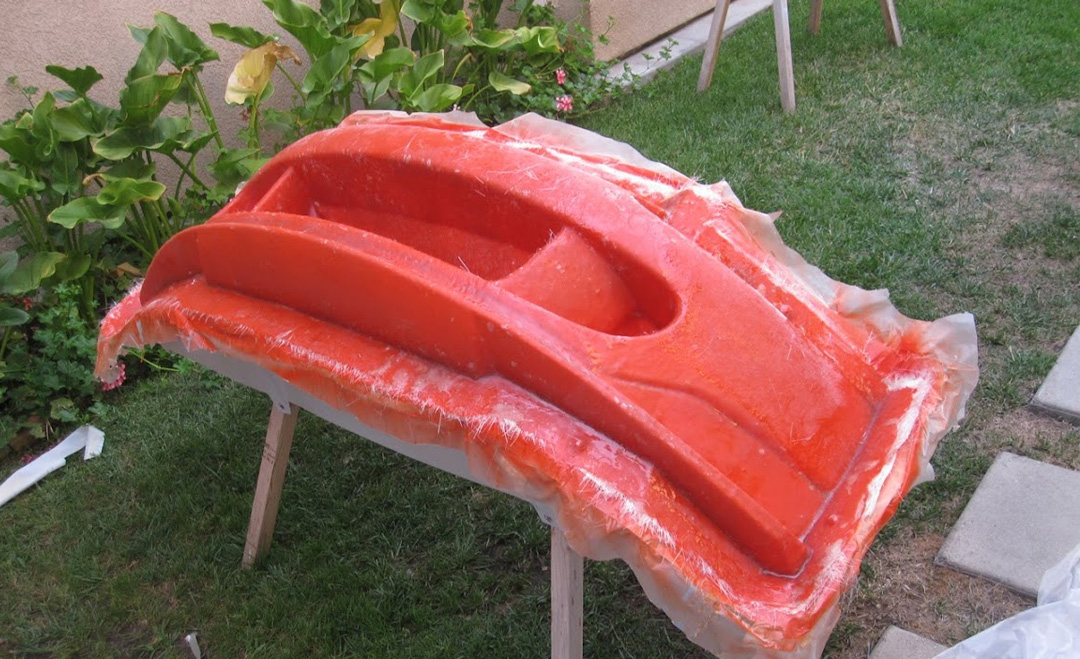
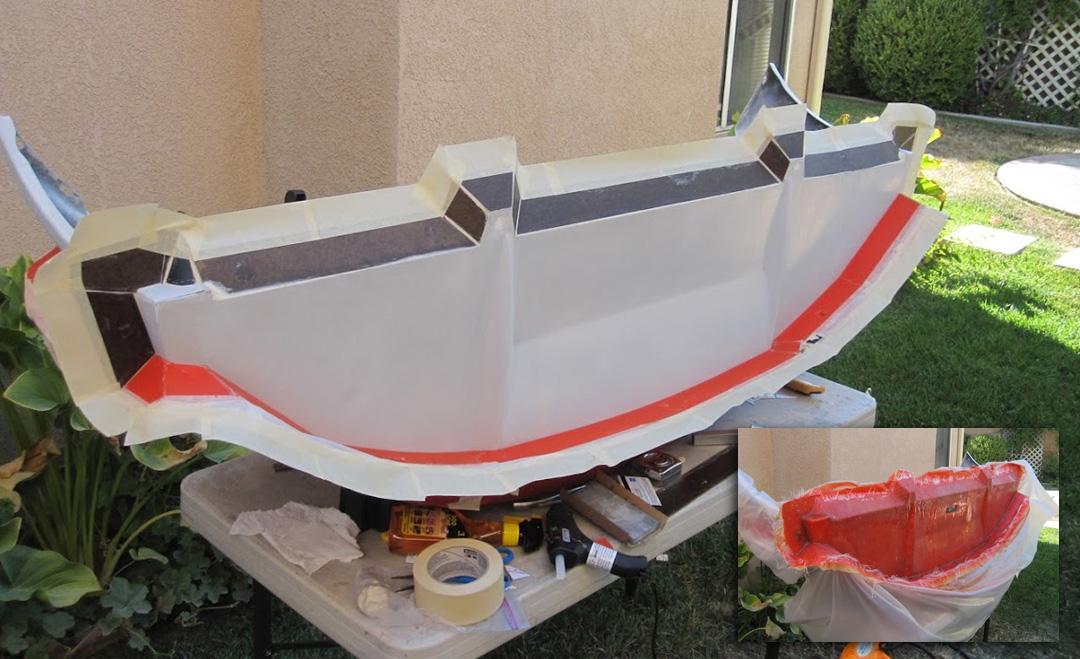
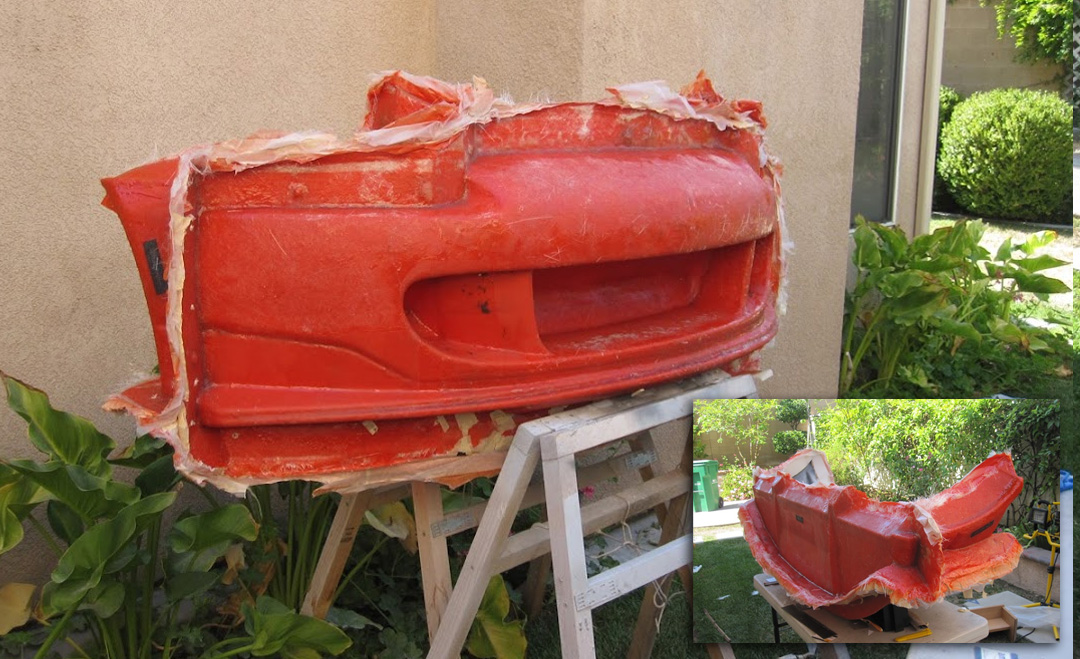
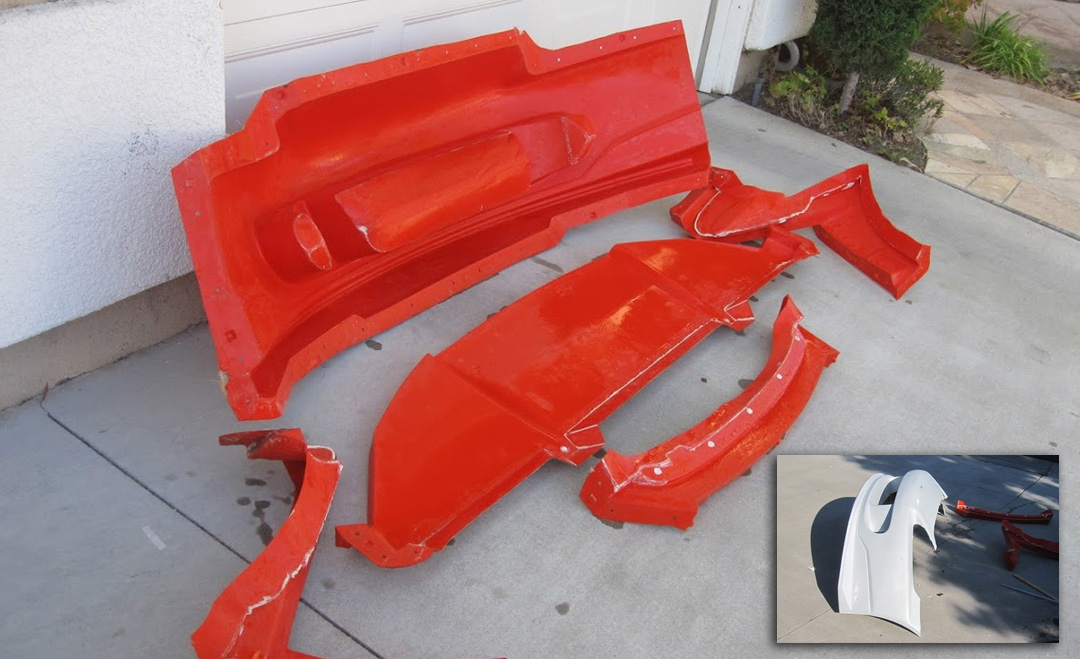
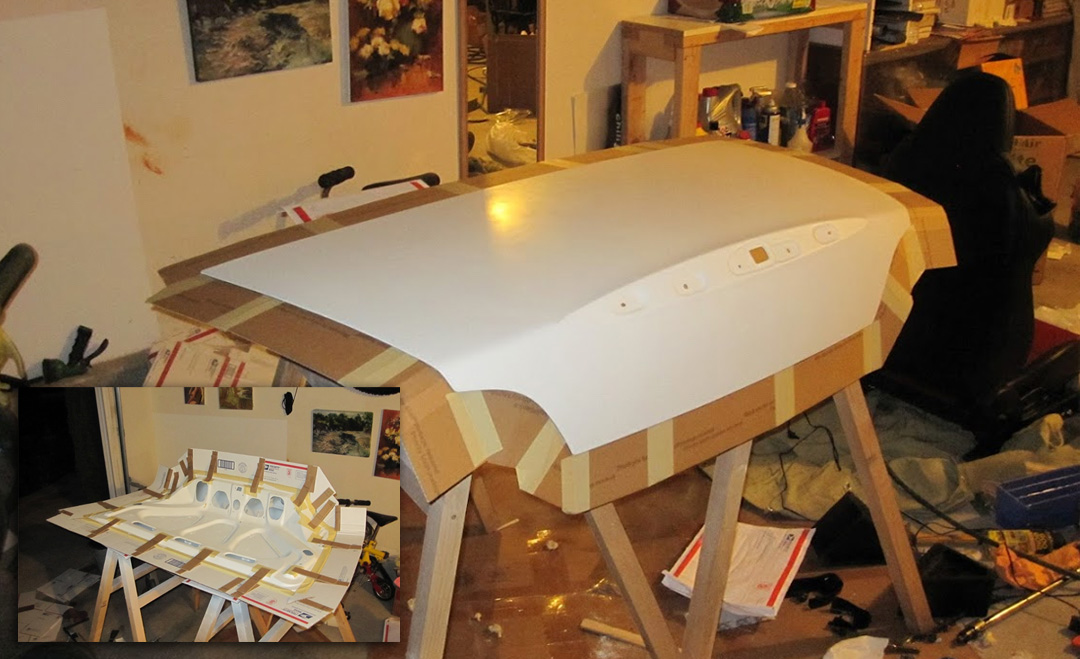
To produce a truly lightweight carbon fiber trunk, I started by modifying a factory OEM part to serve as a perfect master. The keyhole and emblem holes were shaved and smoothed over to create a clean, uninterrupted surface. I then took separate molds from both the exterior skin and the interior structural frame to ensure the final product would be a complete, two-sided part. The final trunk was fabricated using the vacuum bagging method with carbon fiber, achieving a final weight of under two pounds while retaining full structural integrity.
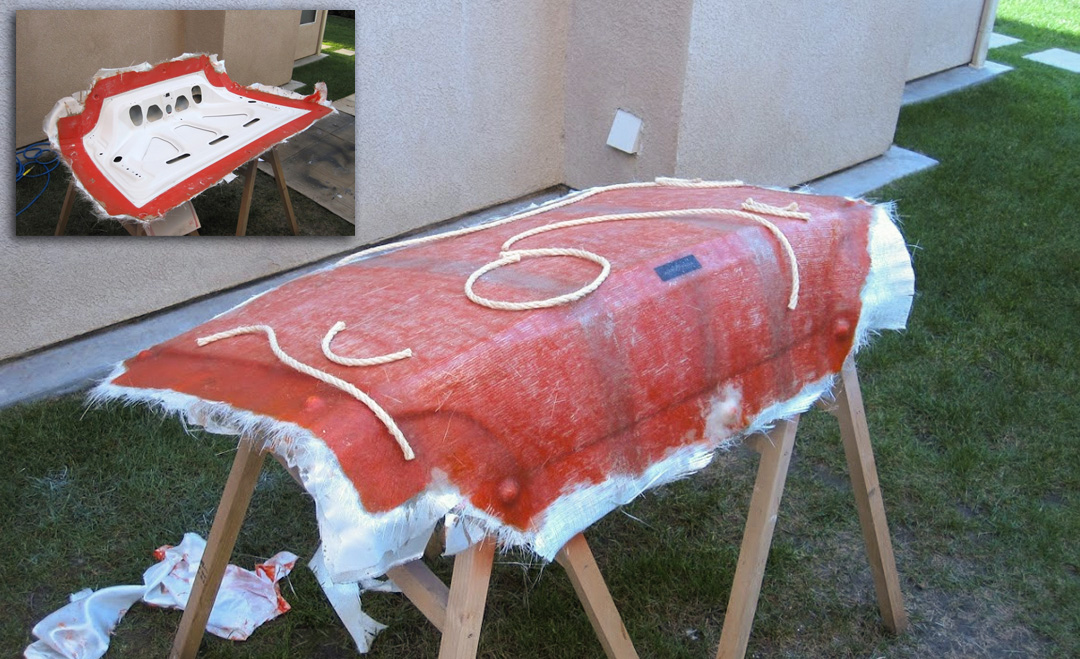
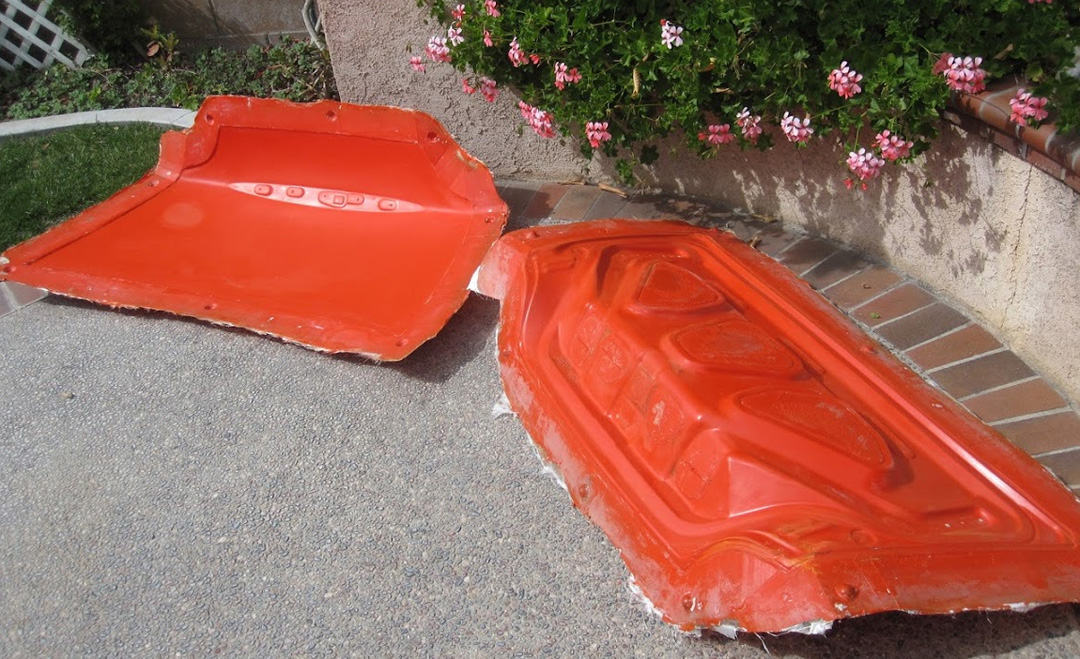
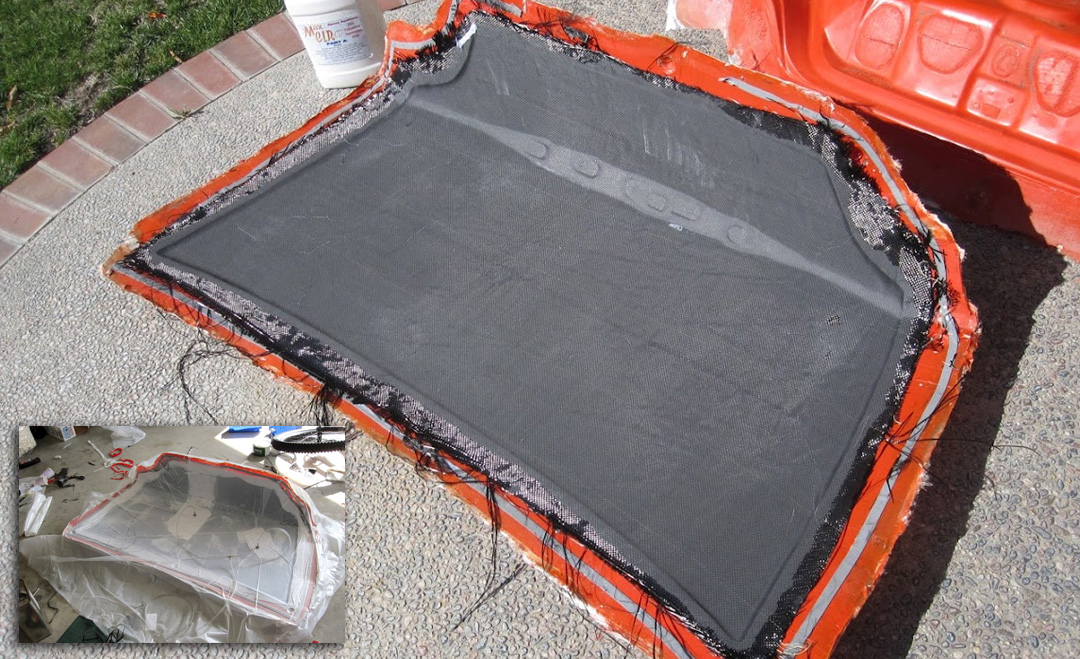
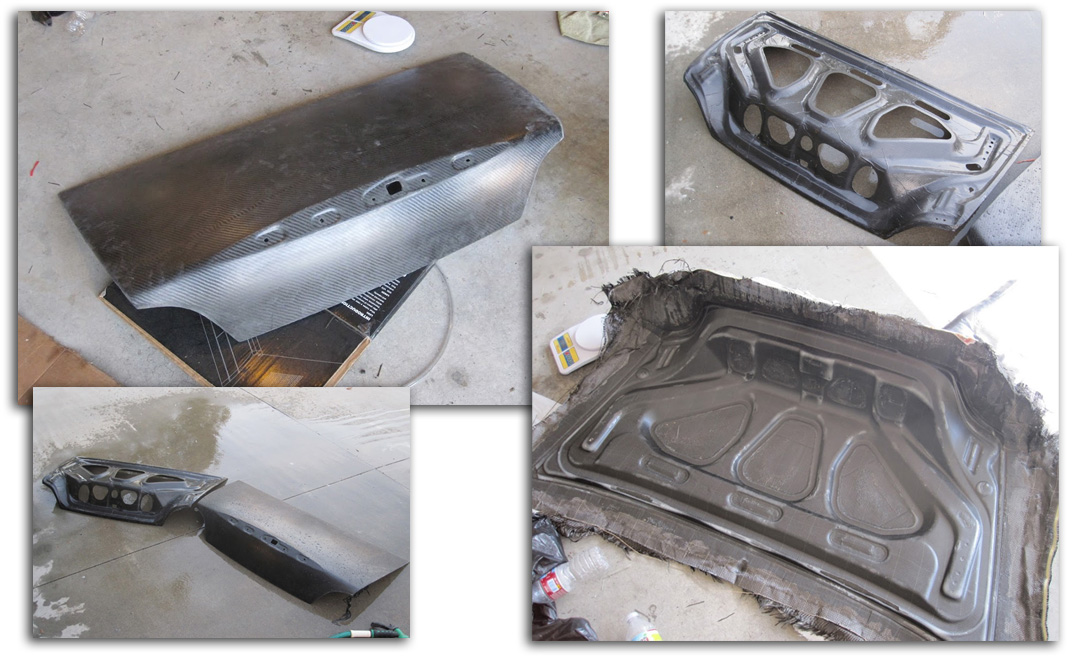
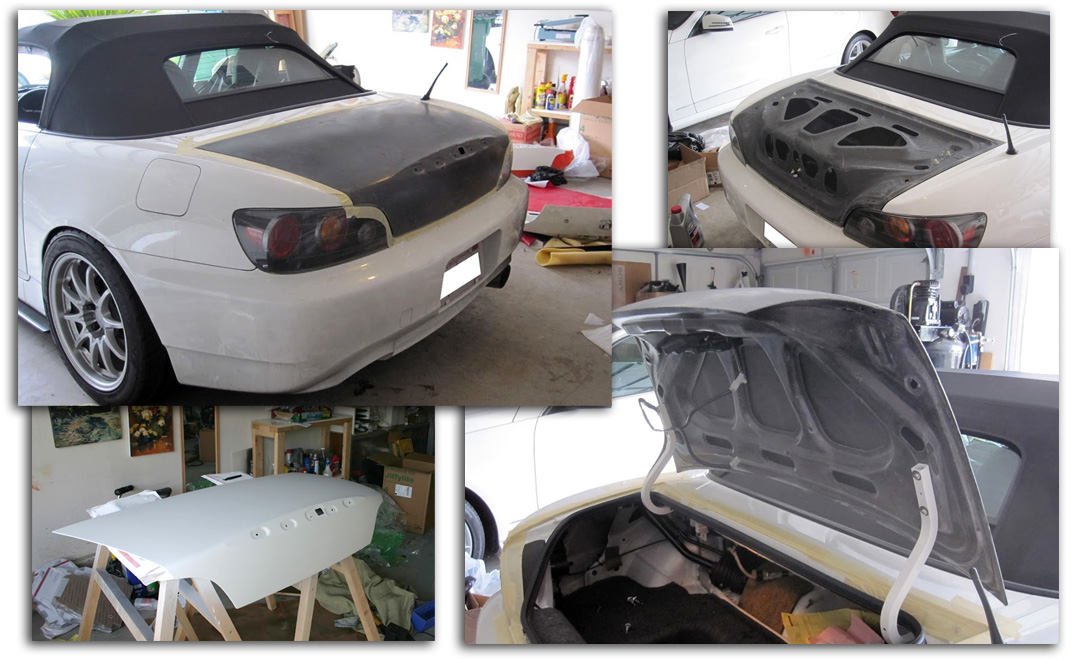
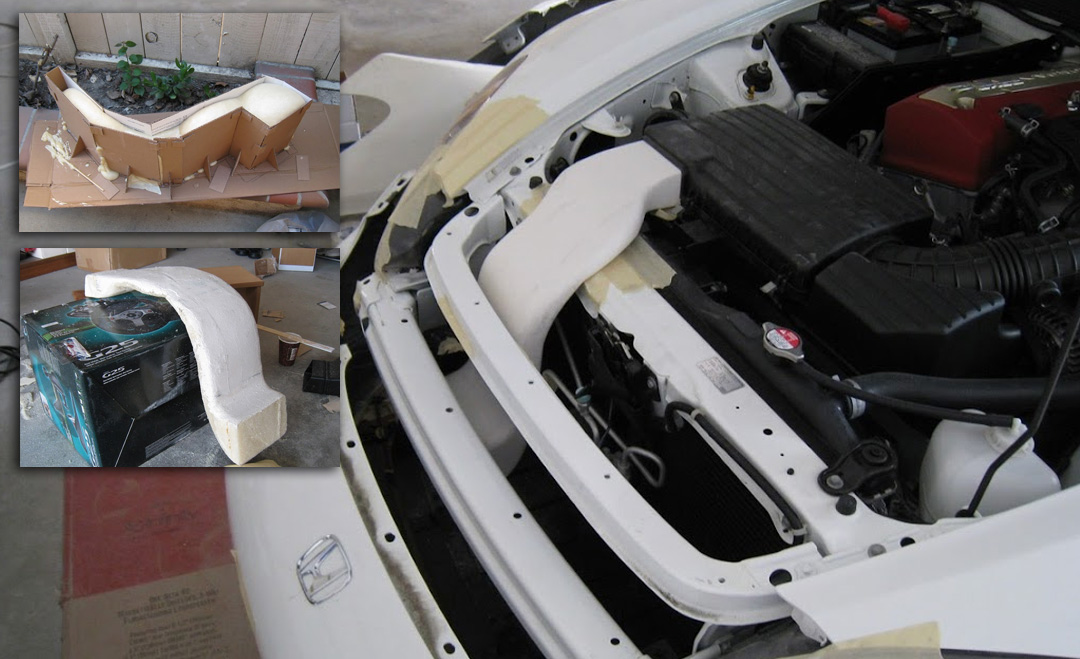
This intake snorkel project demonstrates a workflow from pure hand-crafting to advanced composites. I began by hand-shaping the initial form of an intake snorkel using cardboard and polyurethane foam. Once perfected, this shape was used to create a durable, two-part mold. Using this mold, I then employed vacuum forming techniques to produce a single-piece, hollow carbon fiber intake snorkel. A key design constraint was ensuring a perfect fit with the factory intake box, a goal that was successfully achieved without requiring any modification or cutting of the vehicle's metal body panels.
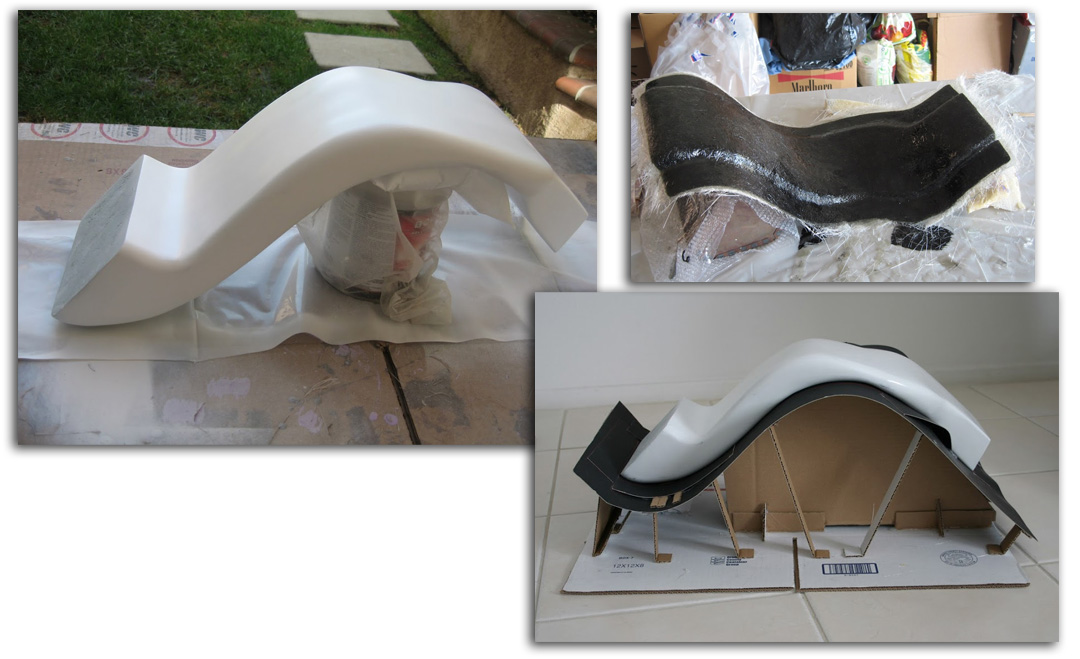
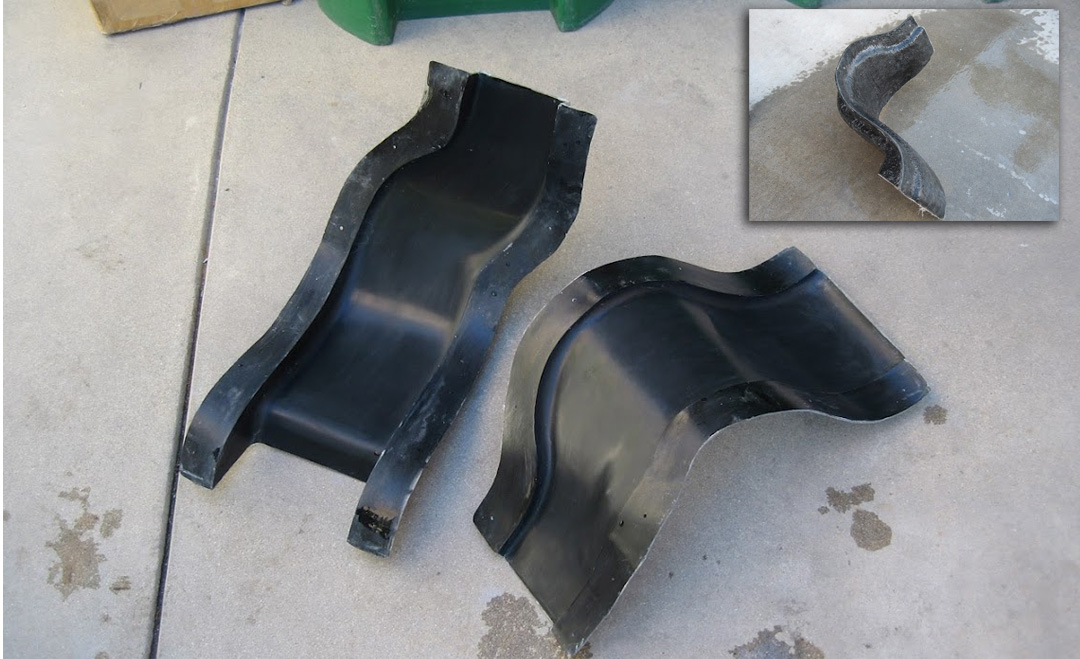
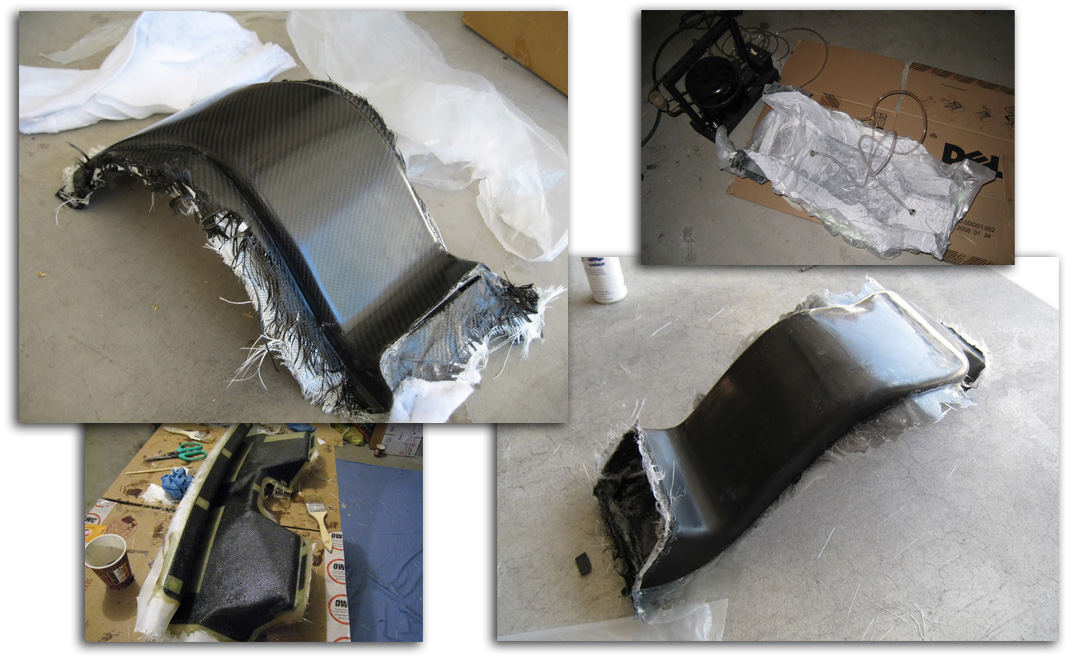
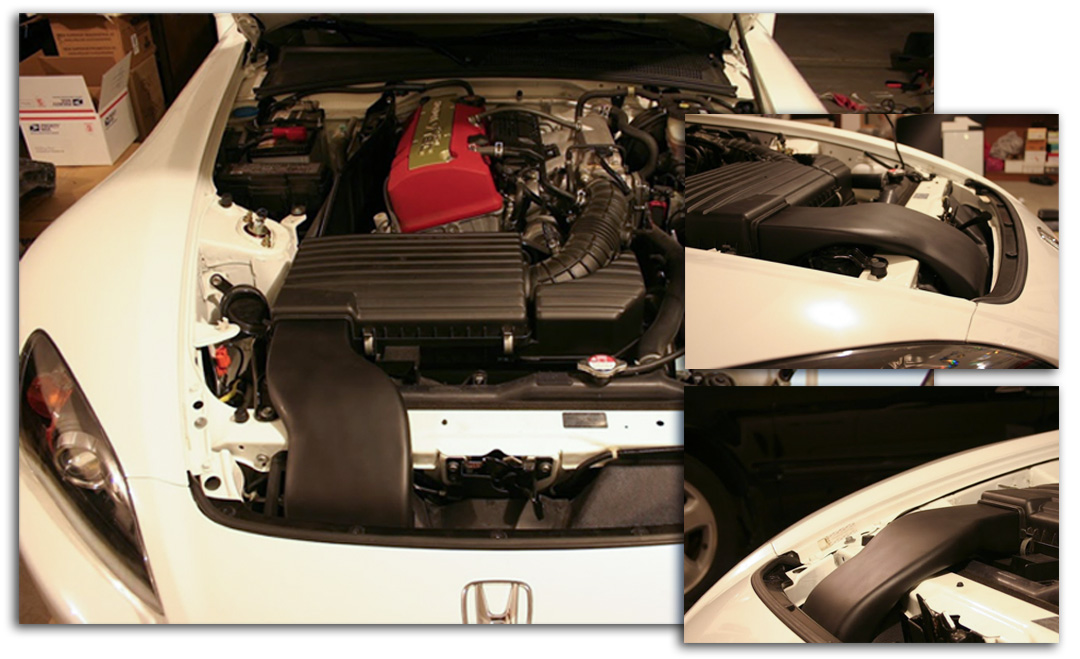
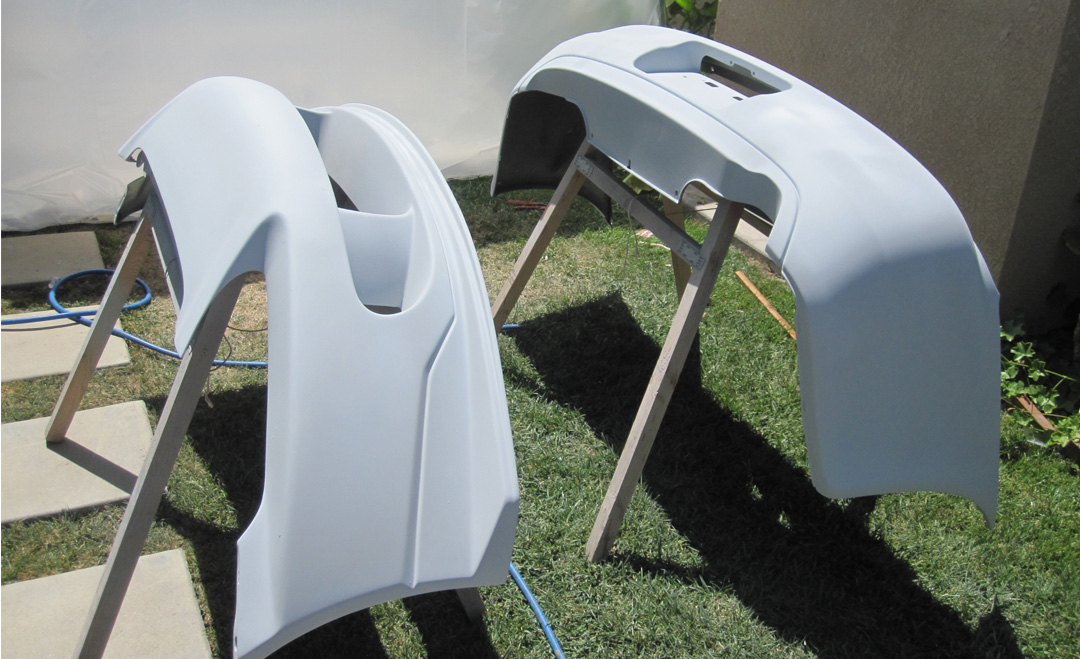
Achieving a professional paint finish without a professional paint booth was the final challenge. My solution was to construct a temporary, makeshift booth from a pop-up canopy, complete with a self-designed filtered intake and exhaust system powered by box fans. This setup allowed me to create a controlled environment where I personally prepped, primered, and spray-painted all the custom body parts, ensuring the final quality was up to my high standards.
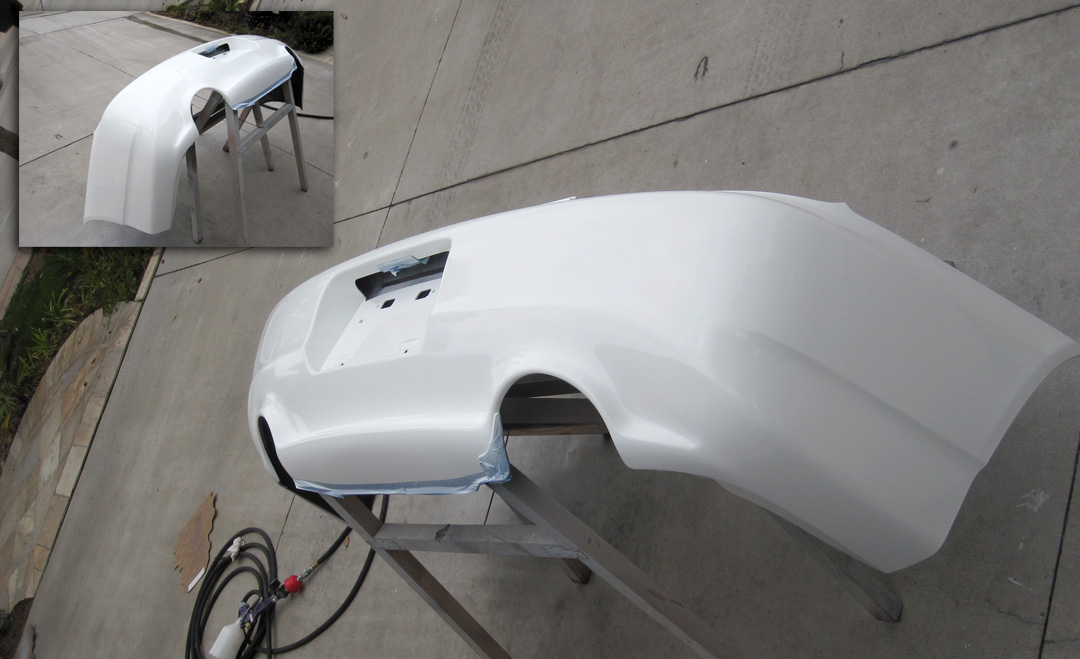
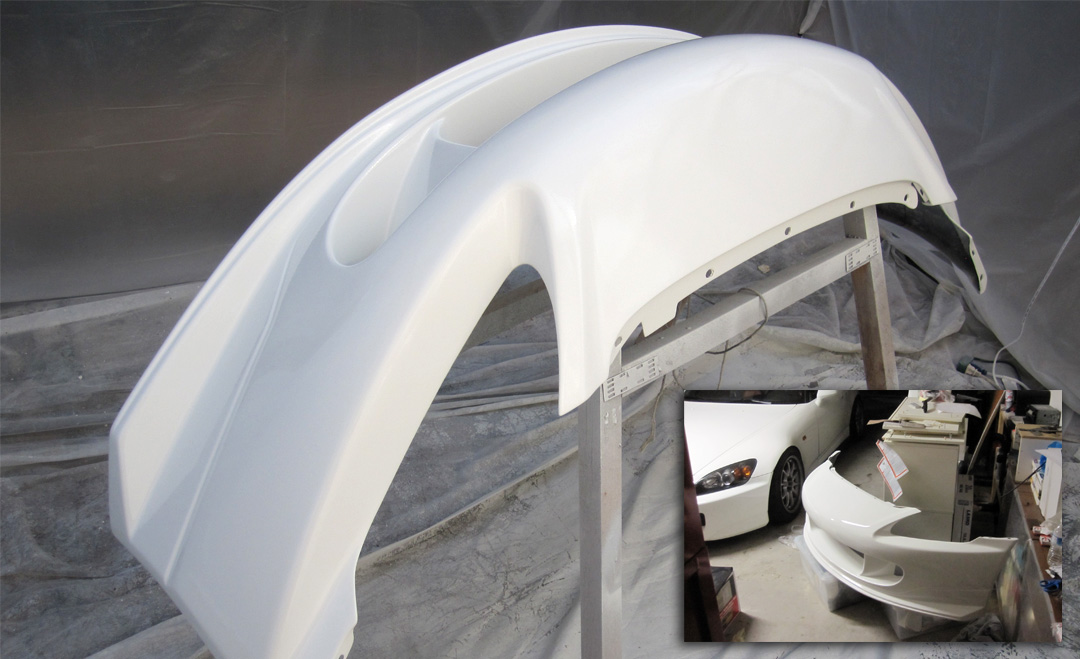
Ultimately, I truly enjoy the intricate challenges presented by mold making and composite fabrication. There's a unique satisfaction in turning a hand-shaped design into a strong, lightweight, and precise final part. For me, the process culminates in the art of automotive painting, which I view as both a science in its technical application and an art in its pursuit of a flawless finish—a discipline that demands patience and a deep commitment to mastering the craft.
To further illustrate these skills, below is a showcase of a few other custom composite accessories I designed and fabricated for this car, many of which were sold as bespoke solutions for other enthusiasts.
Custom intake air box:
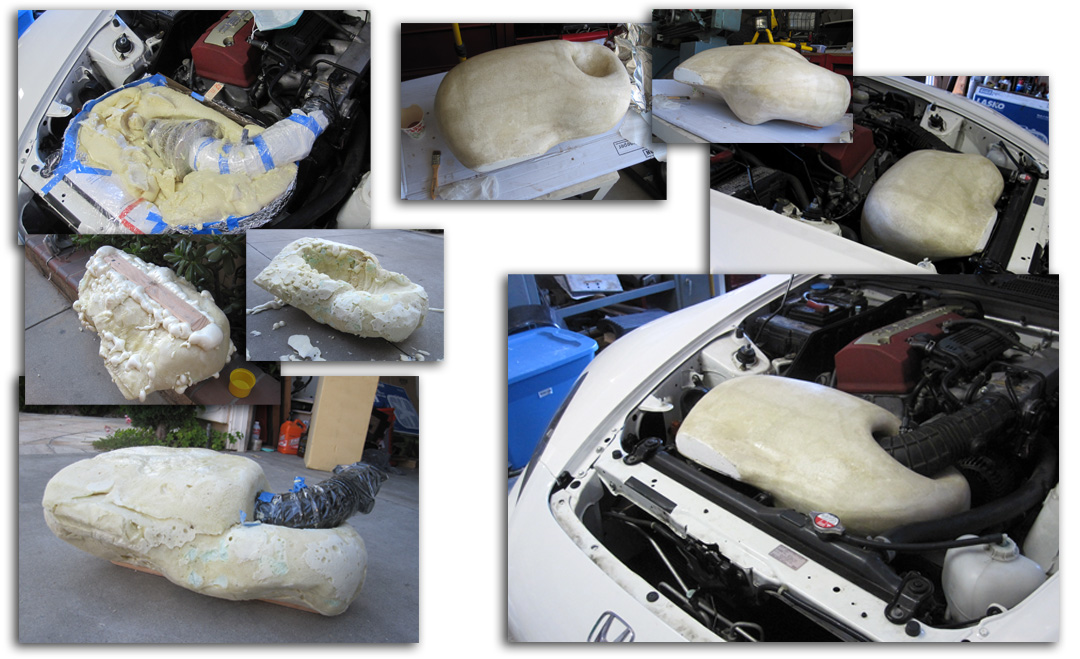
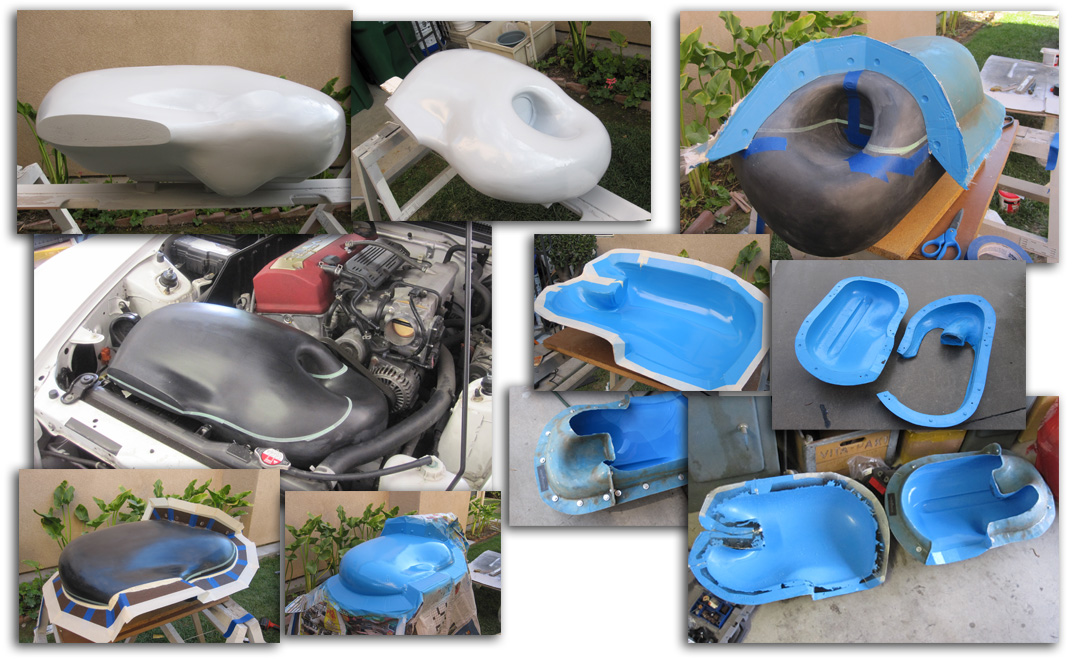
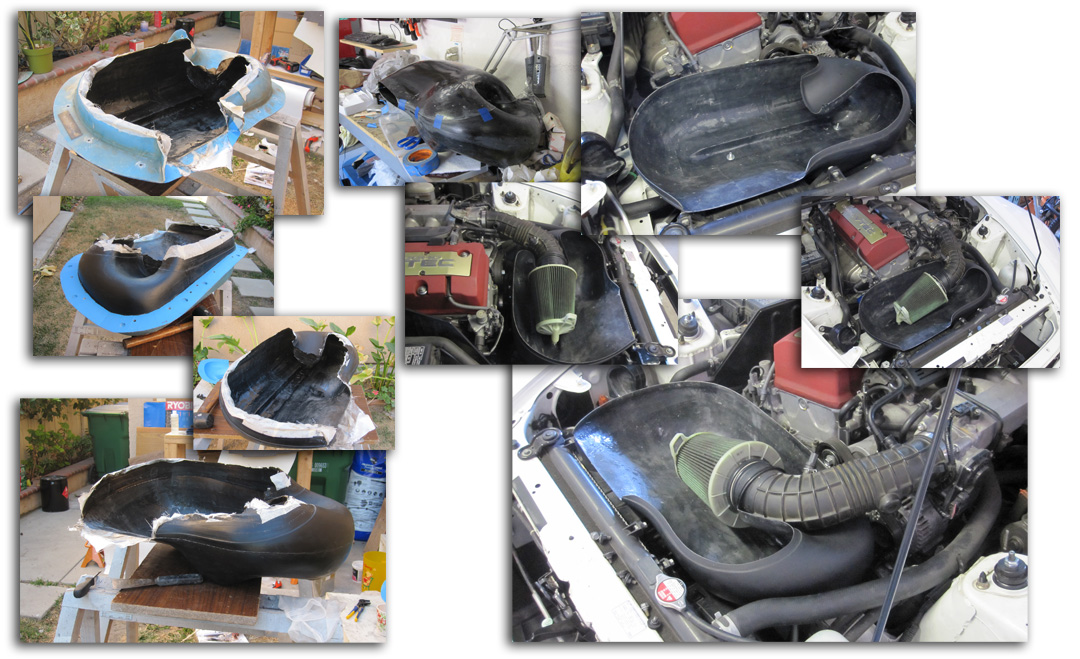
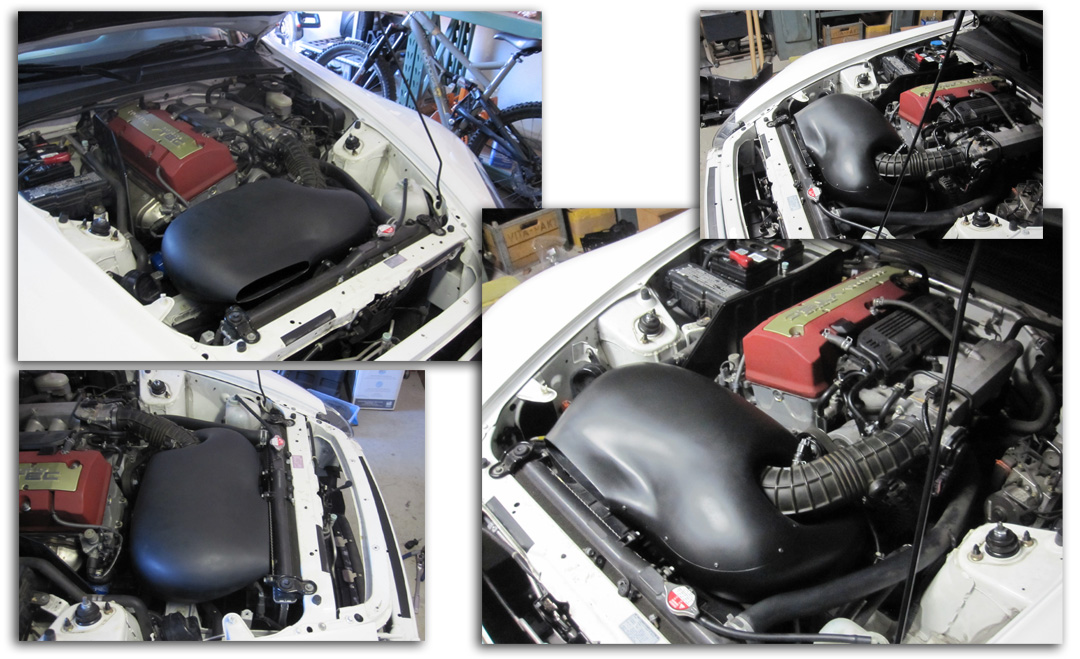
Custom side diffusers:
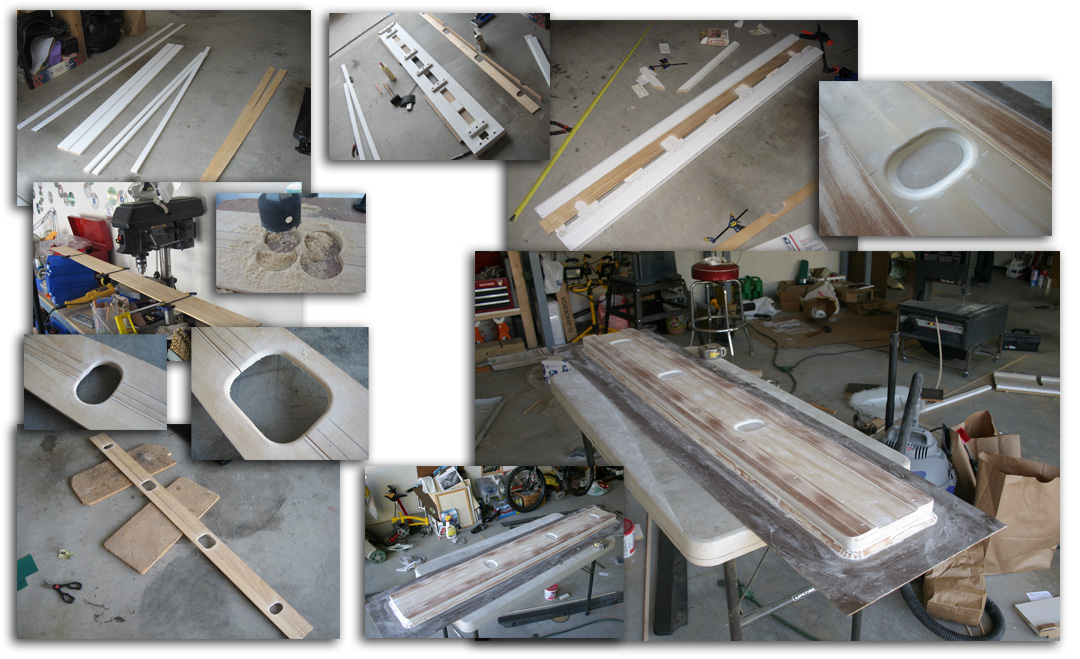
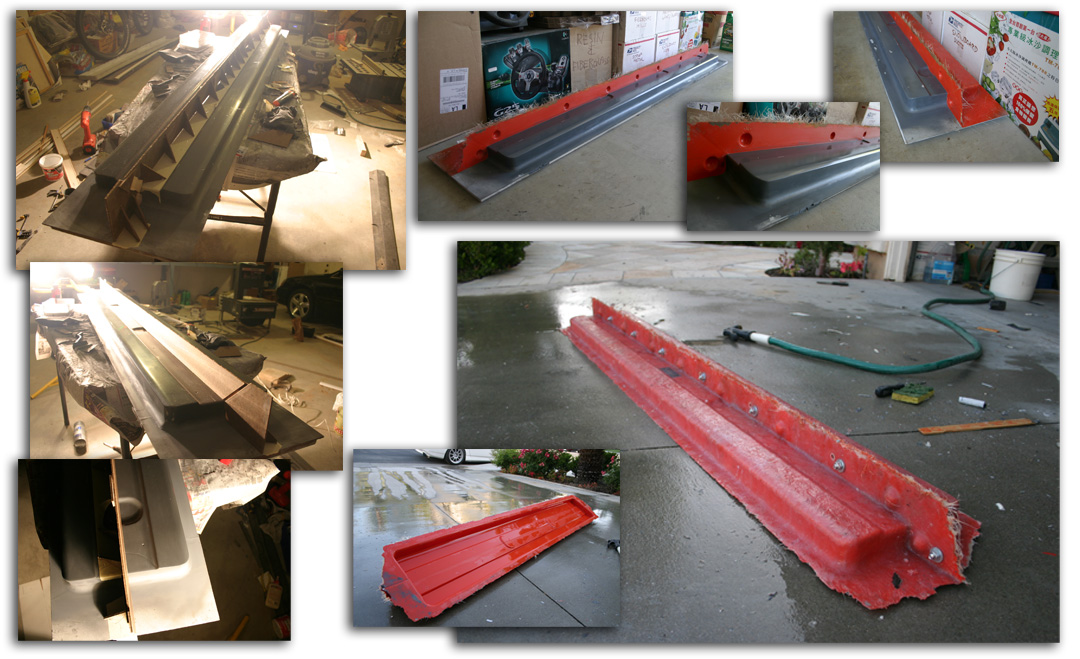
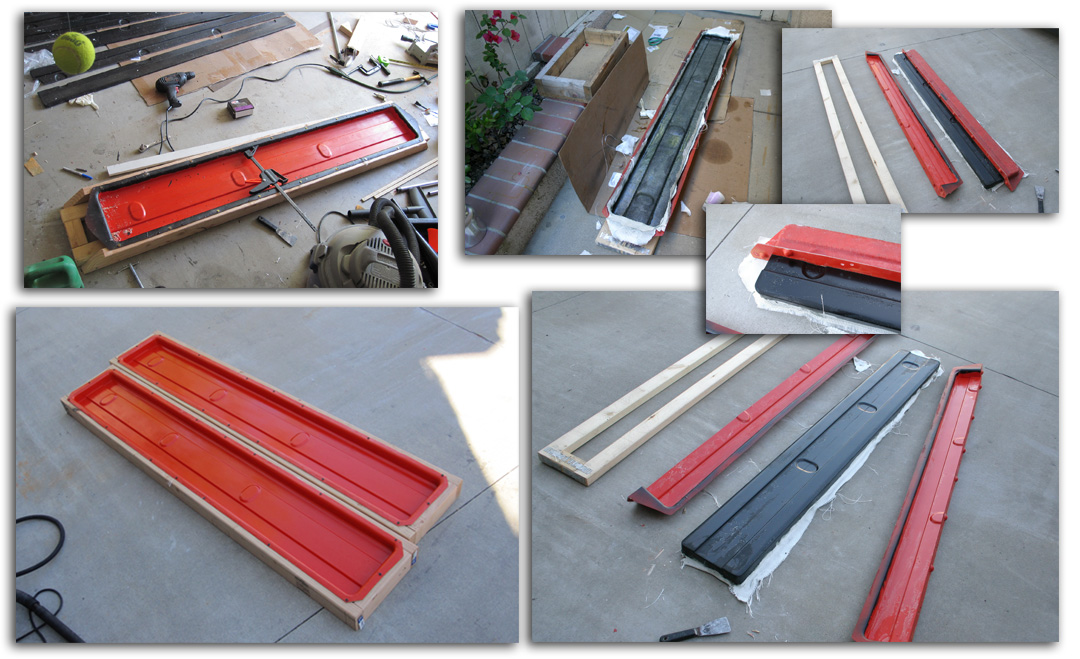
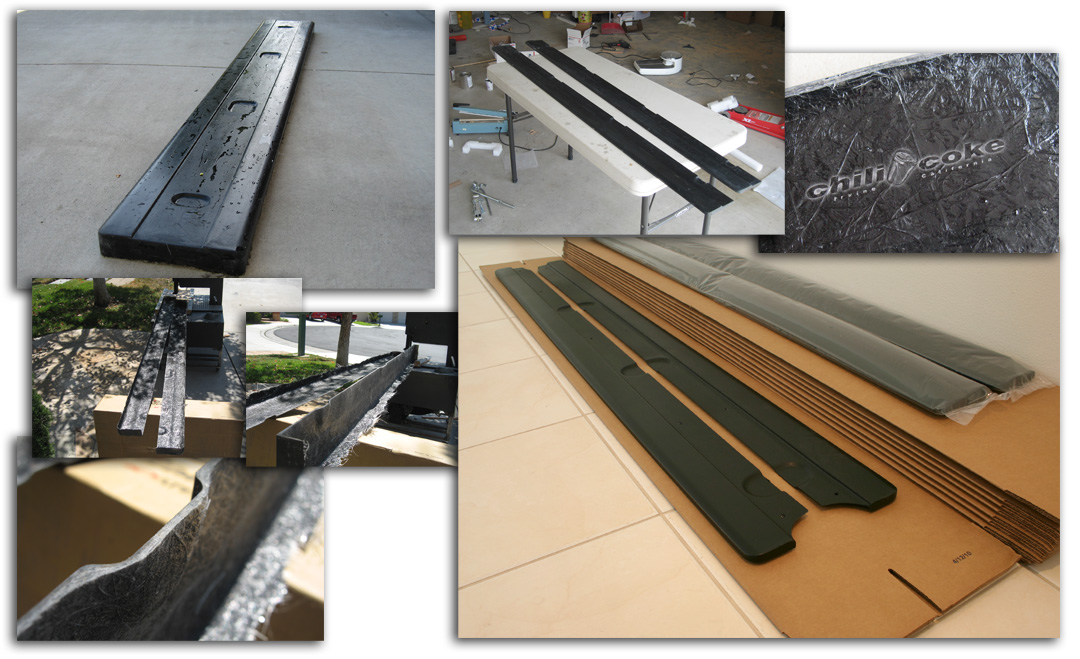
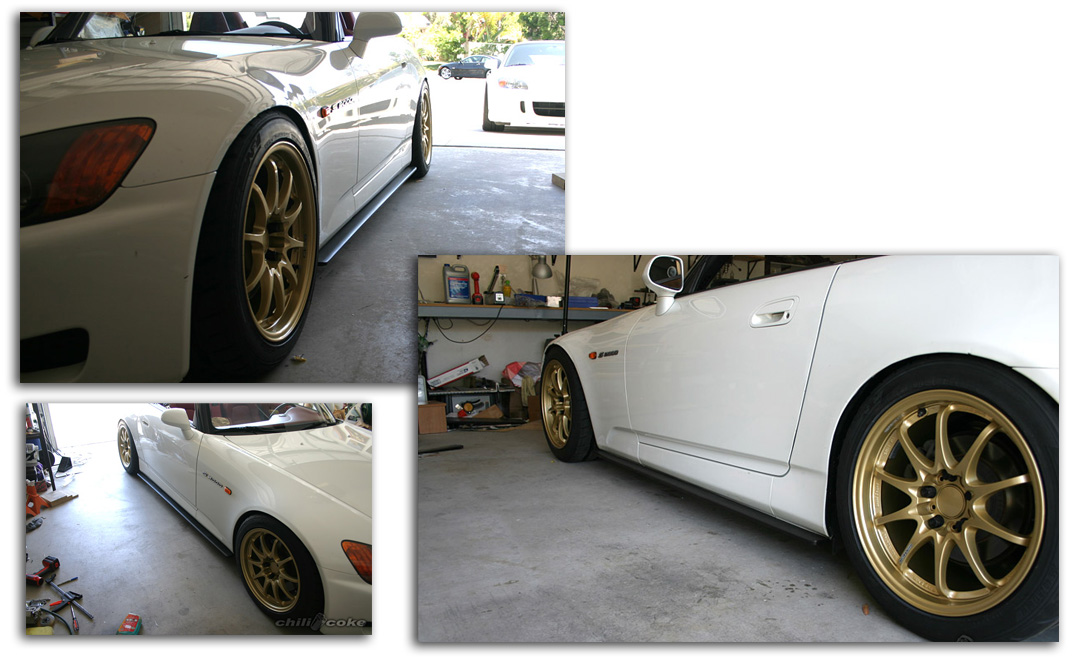
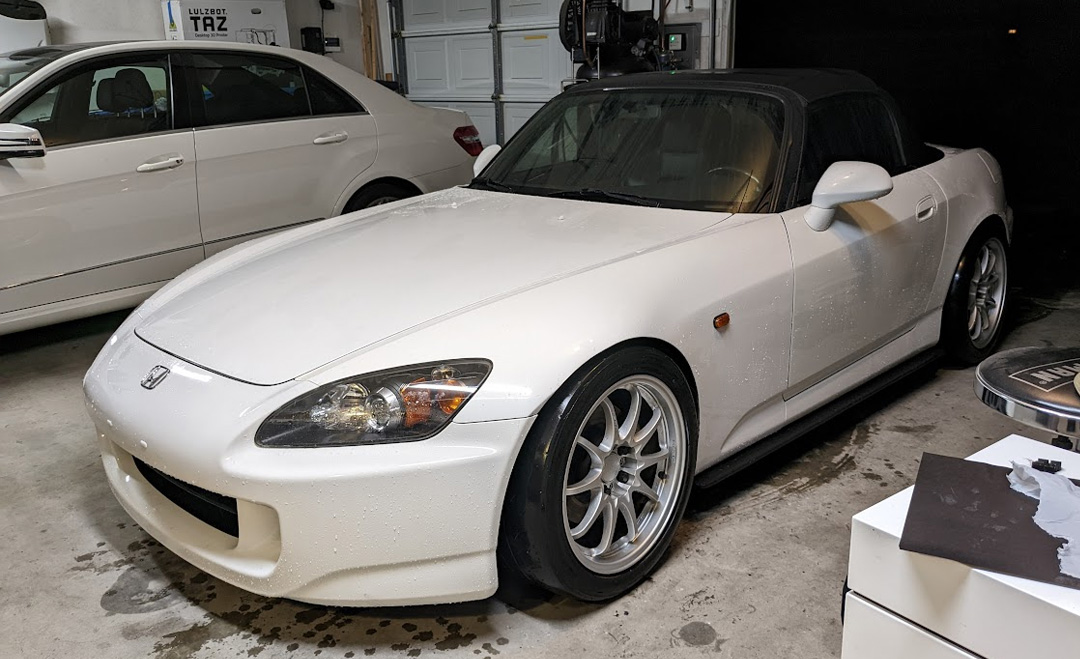
Single exhaust bumper cover:
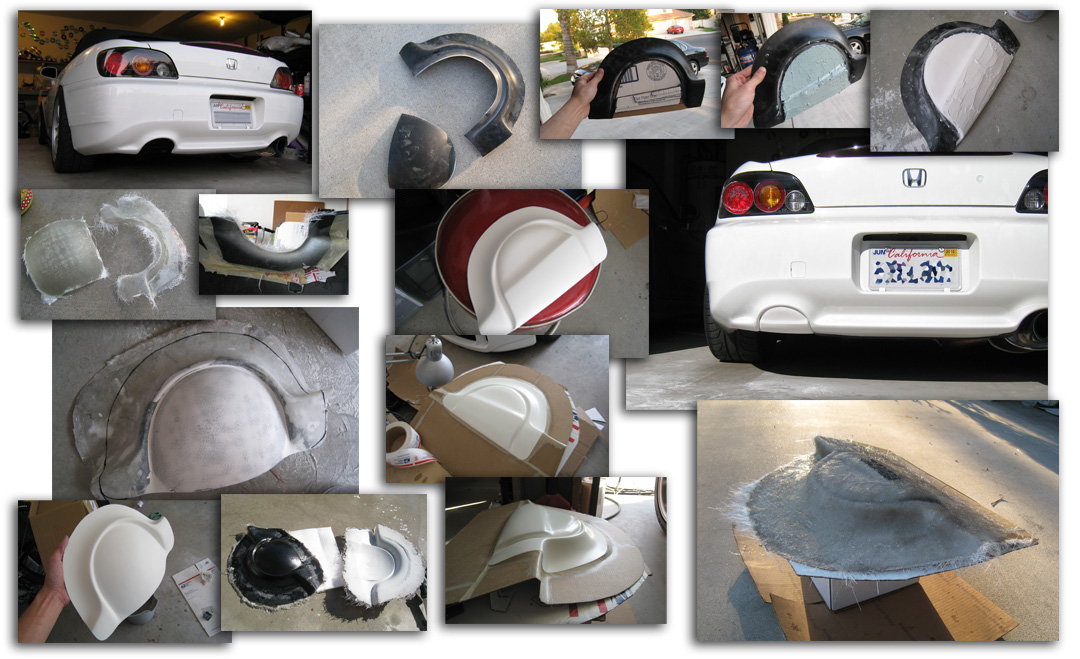
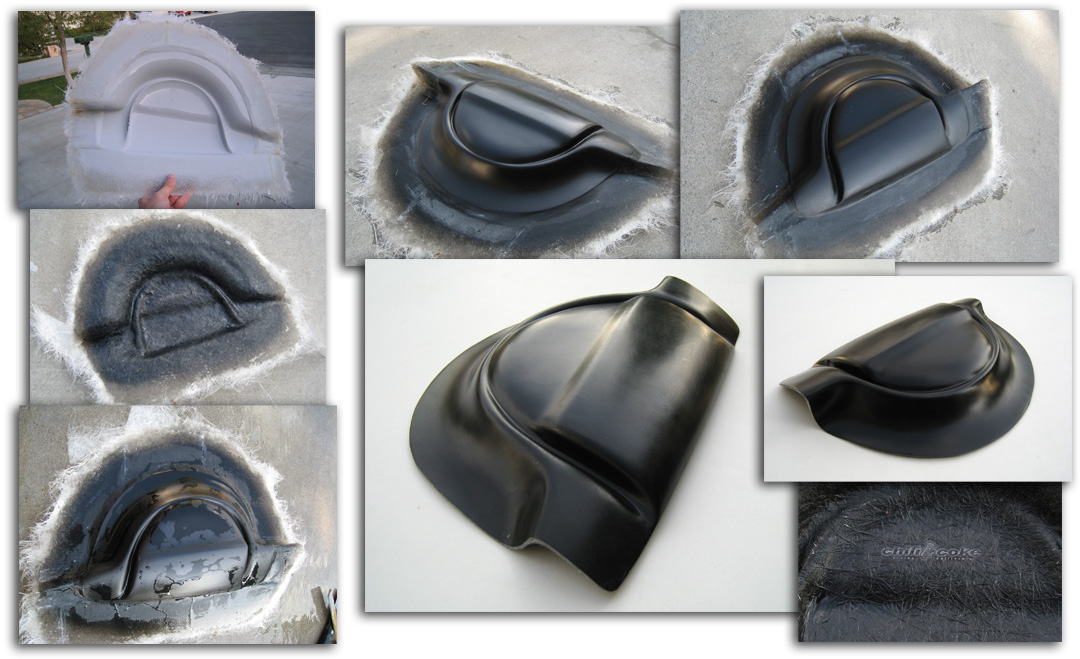
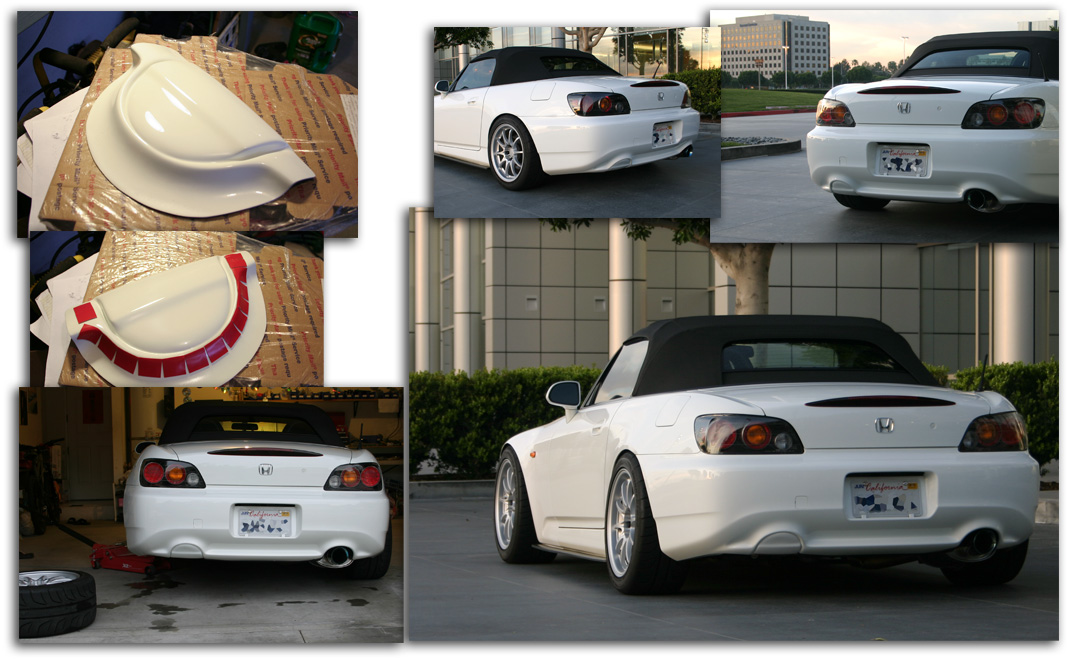
This gallery is just a brief look into some of my favorite projects. There are many more I've completed and documented over the years, and it's impossible to show everything here. If you're interested in seeing more, I would be delighted to bring a more comprehensive collection of my project photos to an interview to discuss my process and passion for building in greater detail.