DIY Racing Drone/FPV Goggle Project
Building and tuning racing drones and FPV goggle systems from the component level, including custom frame modifications and PID tuning for optimal flight performance.
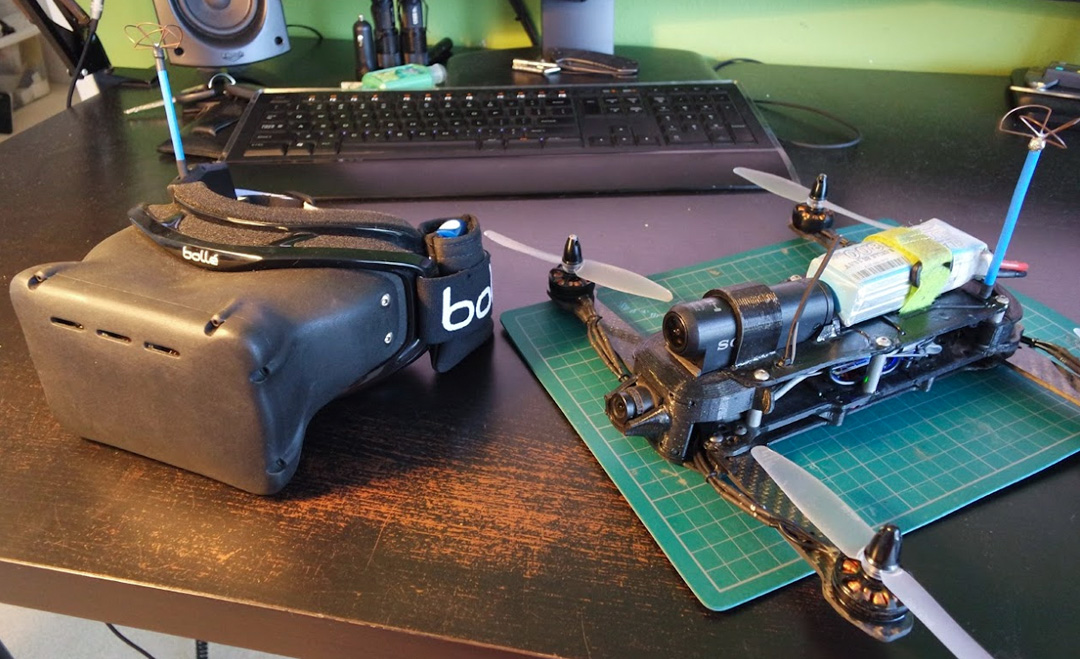
From the outset, this drone was designed with a specific purpose in mind: to be a high-performance cinematography platform capable of carrying a high-quality action camera. Rather than treating the camera as an afterthought strapped to the top, my goal was to fully integrate it into the drone's body. This design philosophy drove the entire project, leading to a custom frame that not only protects the camera but also maintains a balanced, aerodynamic profile for smoother flight.
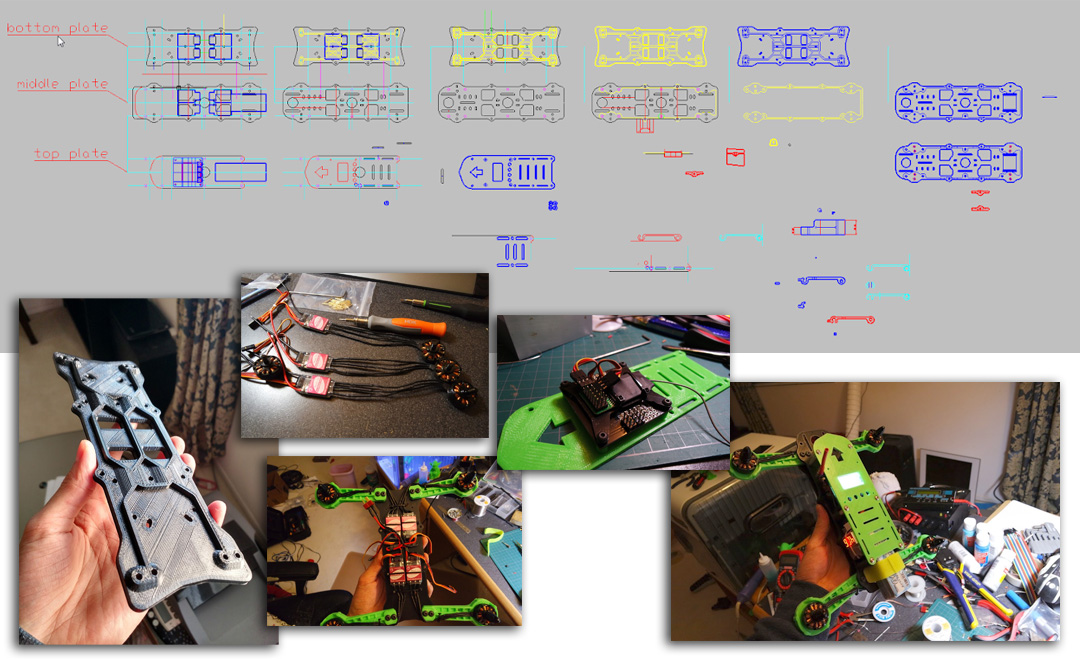
My journey into FPV drones began from scratch, requiring me to build a fundamental understanding of every aspect of quadcopter flight. This meant a deep dive into the core components—motors, electronics, and flight controllers—as well as the complex physics governing flight characteristics, including the critical relationship between the center of balance and center of lift. To accelerate this learning process, I adopted an iterative prototyping approach. The very first drone I designed was a purpose-built trainer with a singular goal: to learn how to fly. Its design was an exercise in minimalism, focused on centralizing all components at the center of lift while stripping away everything non-essential to create a predictable and stable learning platform.
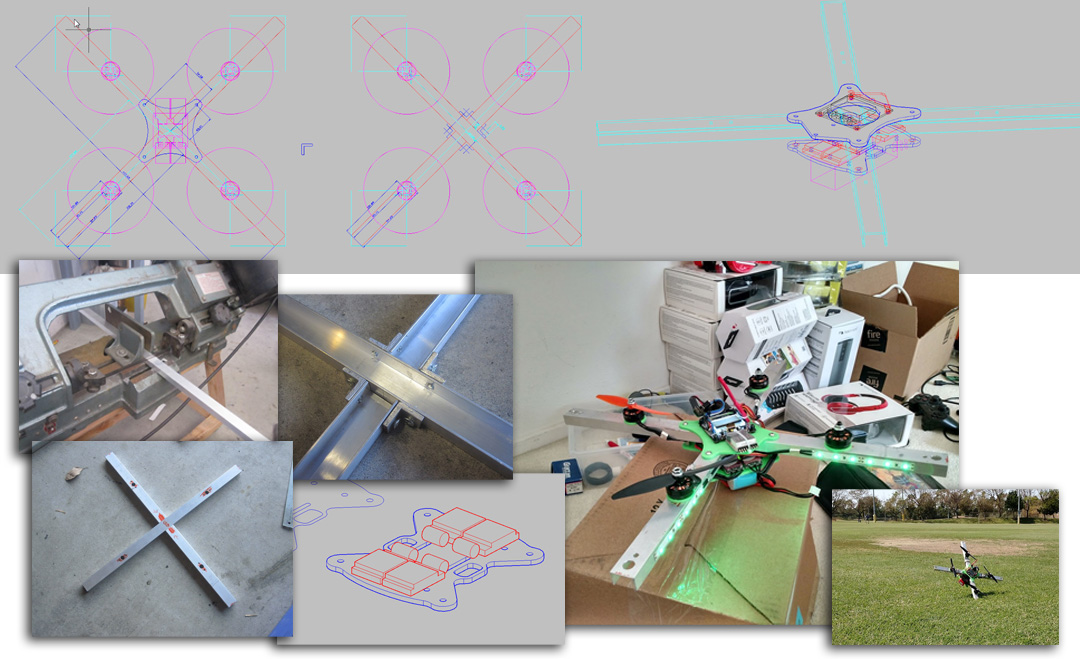
For the second iteration of my drone, my design philosophy evolved to prioritize durability above all else. Having learned how challenging manual FPV flight is without any electronic flight assistance, I knew the next prototype had to be tough enough to survive repeated impacts. To achieve this, I moved to a design centered around an oversized aluminum X-frame. This robust structure was engineered not only to house the components but also to physically protect the propellers from damage, creating a resilient platform built specifically for the rigors of flight training and practice. It didn't take long for the next crash to occur, and the drone survived completely unscratched, immediately proving the value of this robust design philosophy.
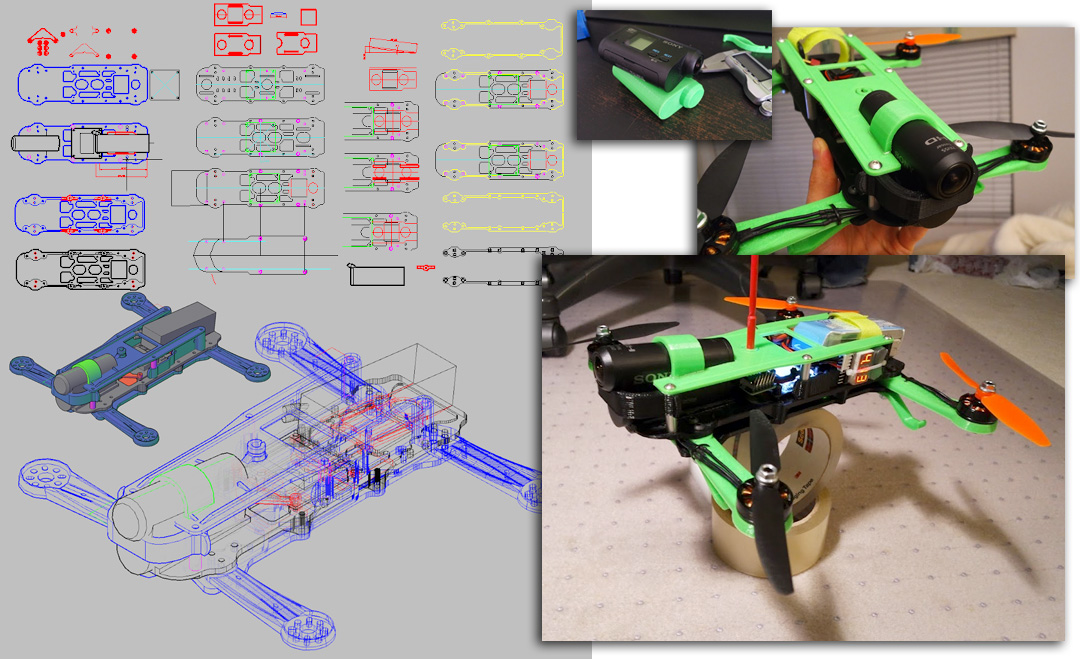
For the third iteration, my design focus shifted back to cleanly integrating a high-quality action camera, this time directly into the drone's nose for a more streamlined and protected profile. To achieve proper balance with the camera's front-mounted weight, I returned to an 'H' frame configuration. This layout was ideal for using the battery as a direct counterbalance at the rear of the frame. The major benefit of this integrated design was a tool-less, quick-release mechanism I developed, which allowed the camera to be securely clipped in or removed in seconds for maximum flexibility in the field.
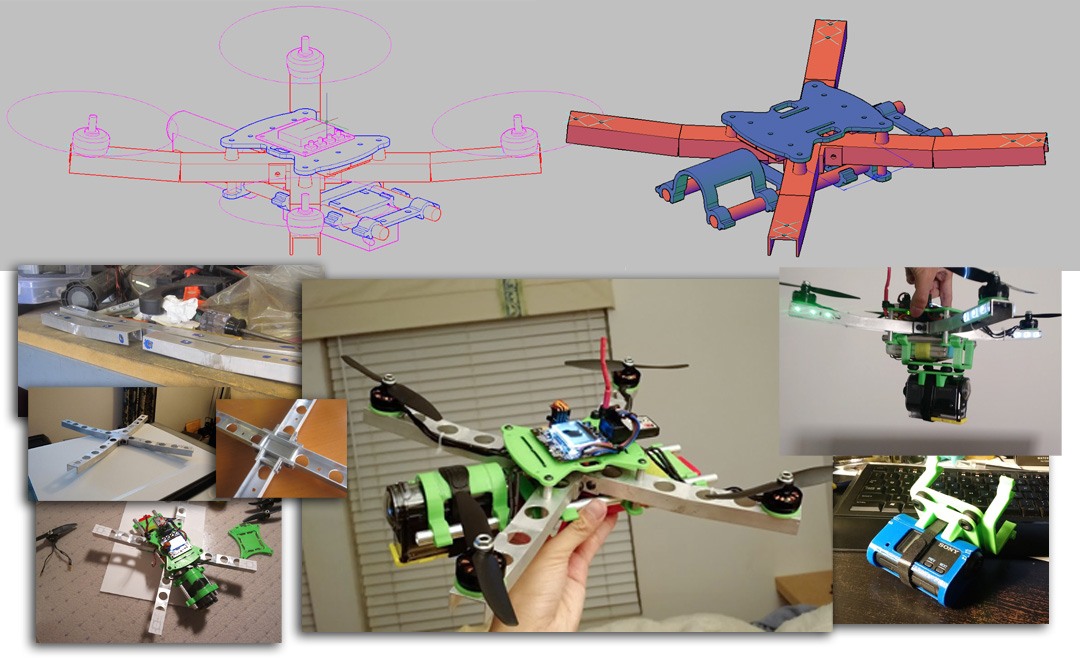
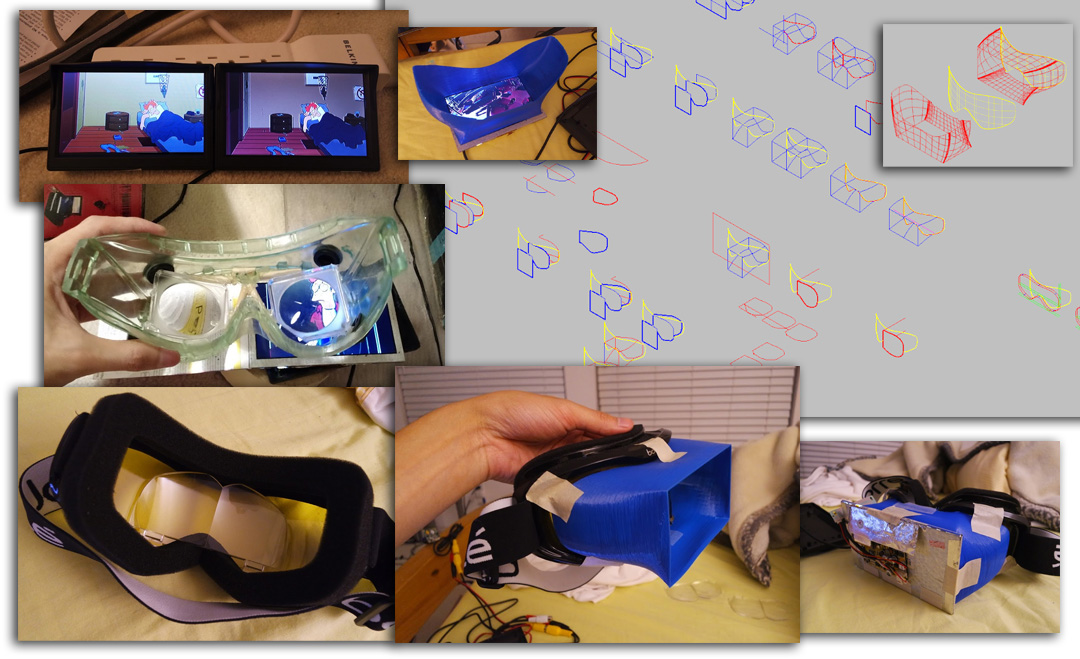
The transition to FPV (First-Person View) flight necessitated a purpose-built prototype for this next iteration. This version had to support the full payload of FPV components—a separate analog flight camera and a video transmission system—while remaining both lightweight and exceptionally sturdy to handle a new, more demanding piloting style. My solution was to evolve the previous aluminum X-frame design. I strategically drilled holes throughout the frame to significantly reduce its weight without compromising structural integrity. To further explore flight dynamics, I also introduced a slight inward angle to each of the propeller mounts, creating a dihedral lift effect to test its impact on stability and handling.
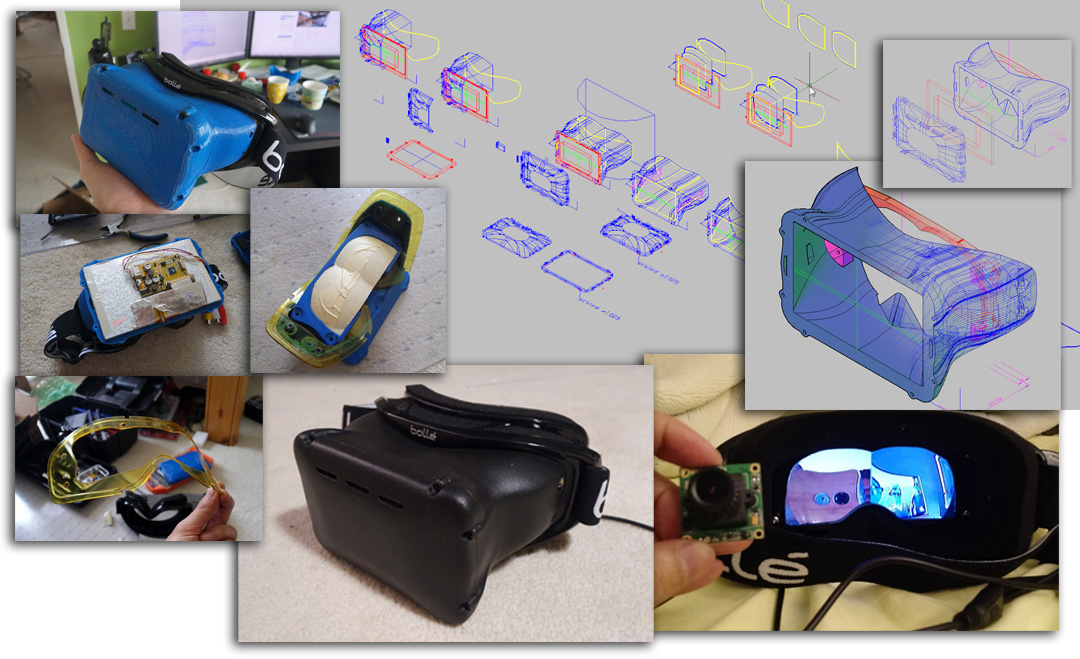
A crucial part of the FPV system is the goggles, but I found the commercially available options to be lacking. They typically had small screens and a restrictive field of view that failed to deliver an immersive flight experience; it felt like looking through a mailbox. Dissatisfied, I expanded the project's scope to include designing my own custom LCD goggles using off-the-shelf components, focusing on comfort, a wide field of view, and reliable reception of the drone's analog video feed.
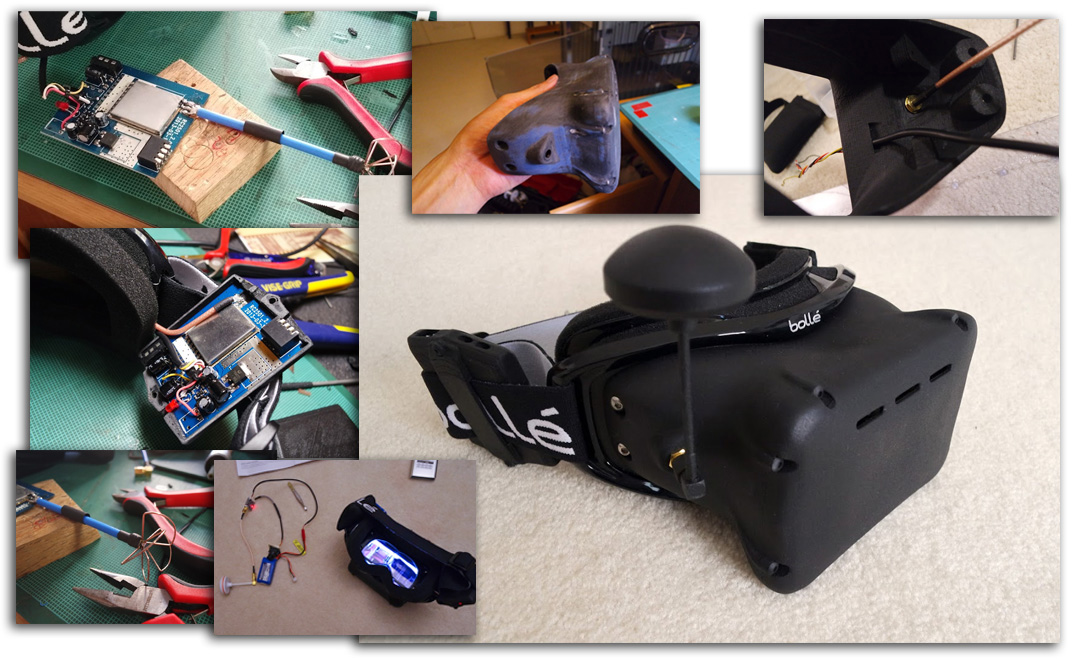
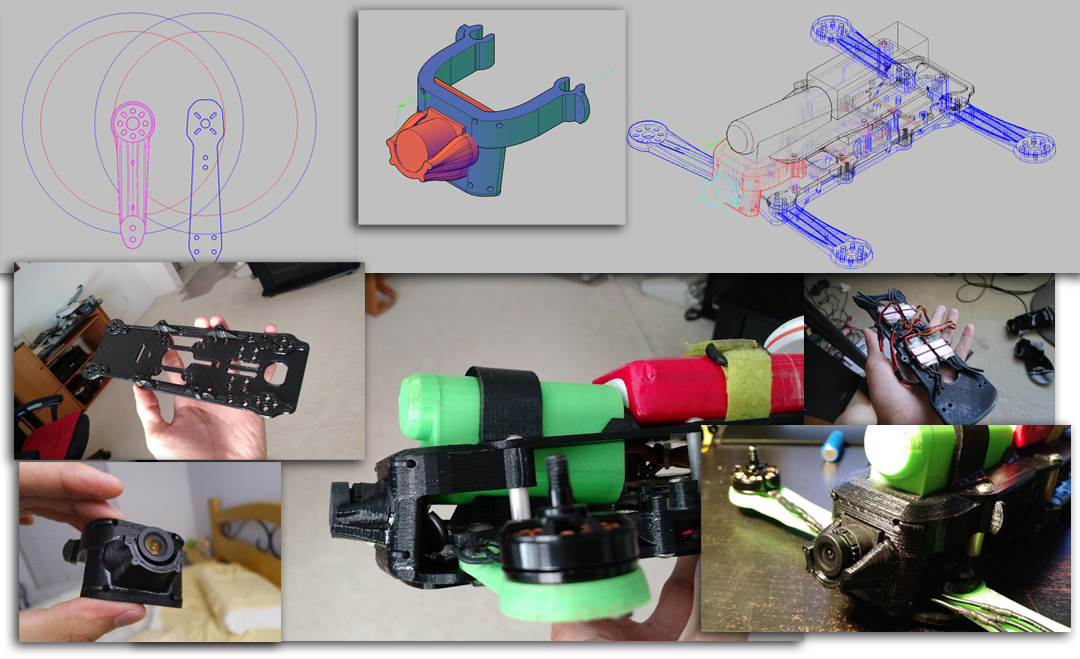
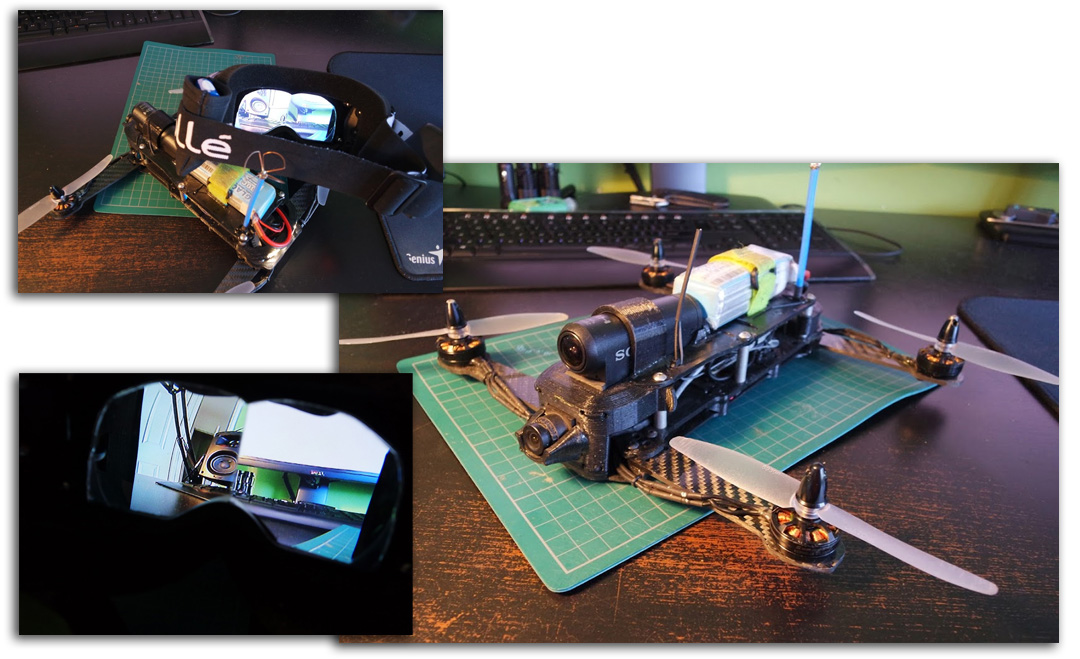
Ultimately, this project was a comprehensive test of skill, demanding a blend of research, iterative design, and hands-on fabrication with multiple materials. Navigating the unique challenges of each stage—from learning flight dynamics to engineering for durability and finally achieving a fully-integrated camera platform—was an incredibly rewarding and educational experience. It stands as a testament to how a high-performance, custom system can be created from the ground up, using clever design and readily available, off-the-shelf components.