The Cockpit That Redefined DIY Racing Rigs
How a focus on true ergonomics and clean design led to a viral DIY project influencing both builders and commercial offerings.
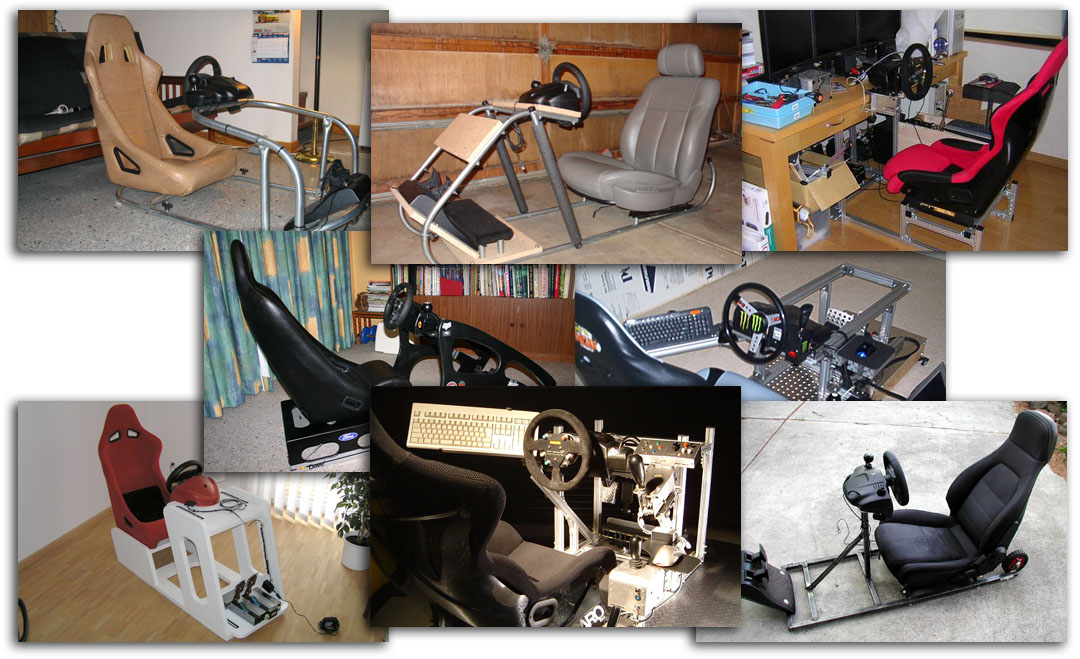
In the early days of home racing simulation, if you wanted an immersive setup, it was a 'DIY or nothing' world, as commercially produced cockpit frames were a rarity. The community was largely split between a few well-resourced individuals capable of elaborate custom fabrication (machining, welding, CNC) and the vast majority of hobbyists who ingeniously used what was accessible—often aluminum extrusions, but just as frequently 2x4 lumber, MDF sheets, or PVC piping. Because this was fundamentally a DIY-driven community, the primary focus was understandably on achieving a functional build, often with very little consideration given to sleek visual design or true ergonomic principles suitable for a home environment.
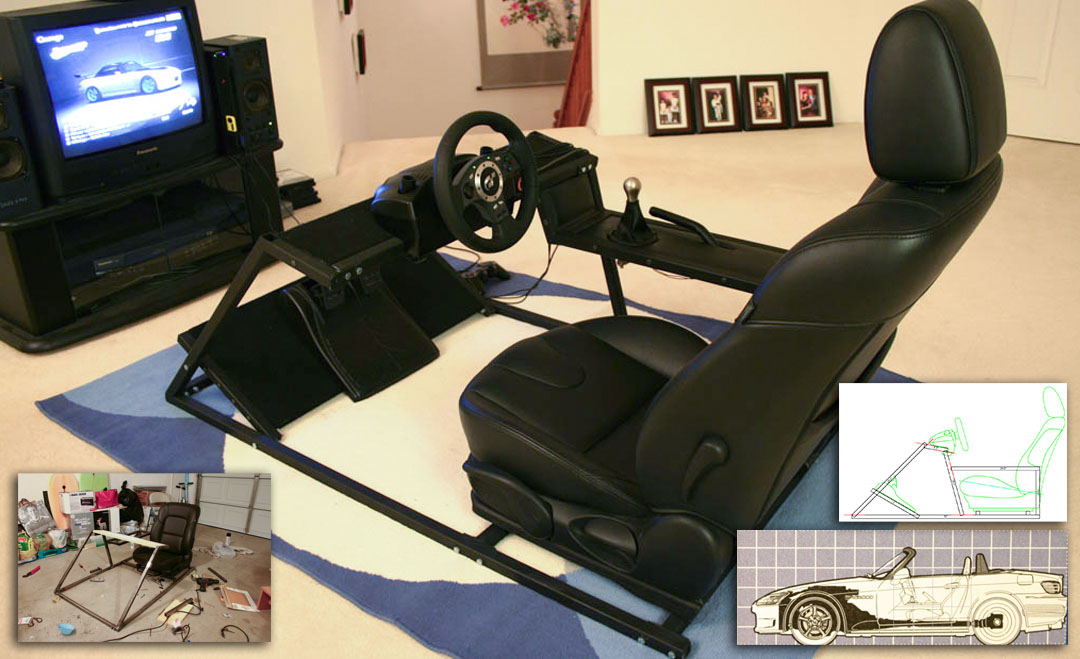
This was my first cockpit build. Its seating position was directly inspired by the Honda S2000, using the car's side profile diagram drawing from Road and Track magazine as a reference; the goal was to efficiently use the least amount of square tubing to achieve the correct position and angles for the seating position, steering wheel, pedals, and shifter.
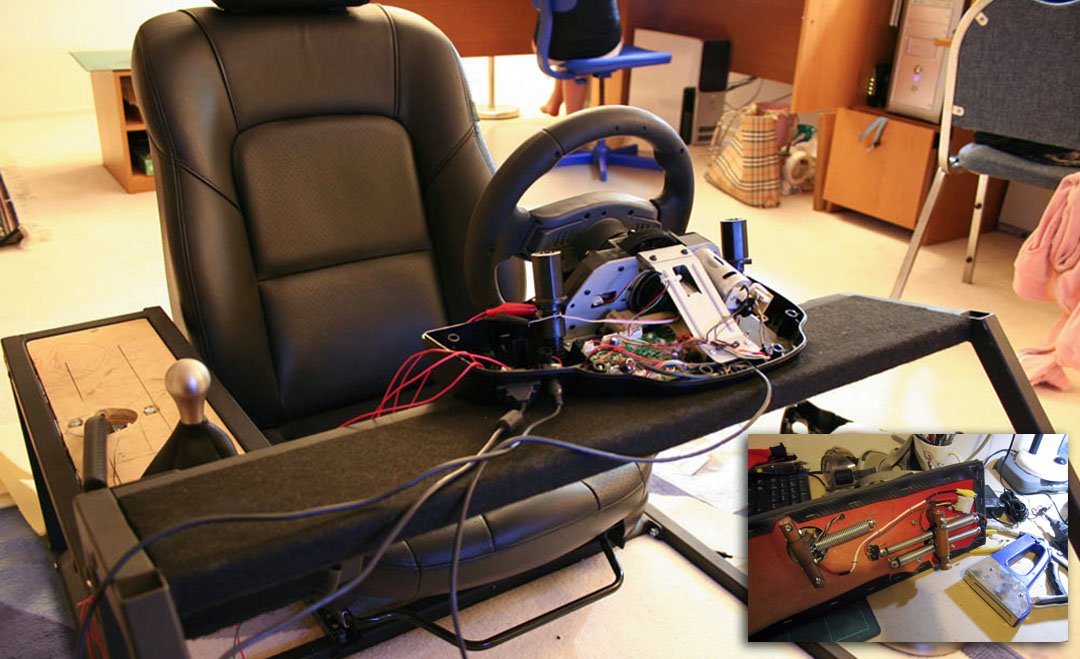
Working with significant budget constraints on this first build also meant innovating with the existing hardware. The steering wheel controller I was using didn't support an external shifter or handbrake lever, common components for a more realistic simulation. My solution was to construct these crucial controls myself from hot water copper pipes, triggering microswitches that were soldered directly onto the controller's internal printed circuit board (PCB) to complete the circuit as custom controller inputs.

My initial cockpit videos on YouTube achieved unexpected popularity, becoming some of the platform's most viewed in the racing sim category at the time. This success coincided with the release of a new generation of racing simulators and more advanced steering wheel controllers. This convergence presented a clear opportunity to leverage my insights and develop a completely new cockpit from the ground up, featuring revised geometry to incorporate new controller dimensions and integrate features previously unfeasible.
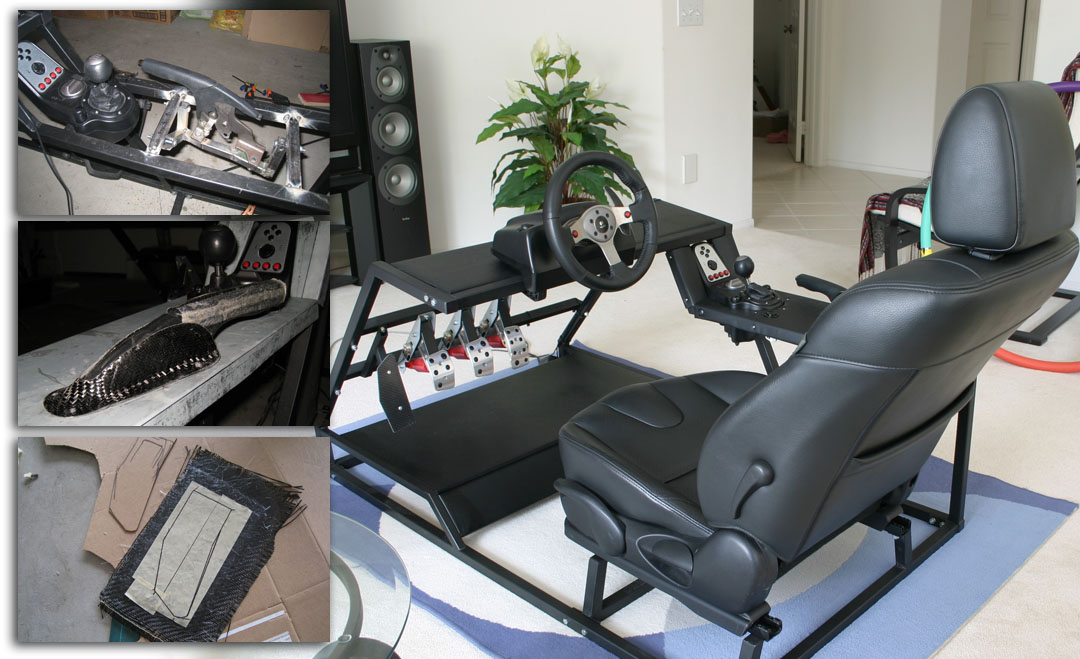
For this new cockpit, I further refined its ergonomic precision and functional realism. I re-designed the seating geometry to perfectly mirror that of a real car, complementing it with modified reverse-mounted pedals for more realism. Additional upgrades involved integrating a complete, functional handbrake assembly sourced from a production vehicle. This build became my platform for learning to work with new materials and construction methods: I MIG welded the core frame for maximum stiffness while incorporating a bolted-tab design for future disassembly. I then custom-fabricated the center console forming sheet steel to shape and upholstered it with foam-padded automotive vinyl. As a final touch, and to expand my experimentation with composites, I crafted the handbrake lever trim and dead pedal from hand-laid wet carbon fiber.
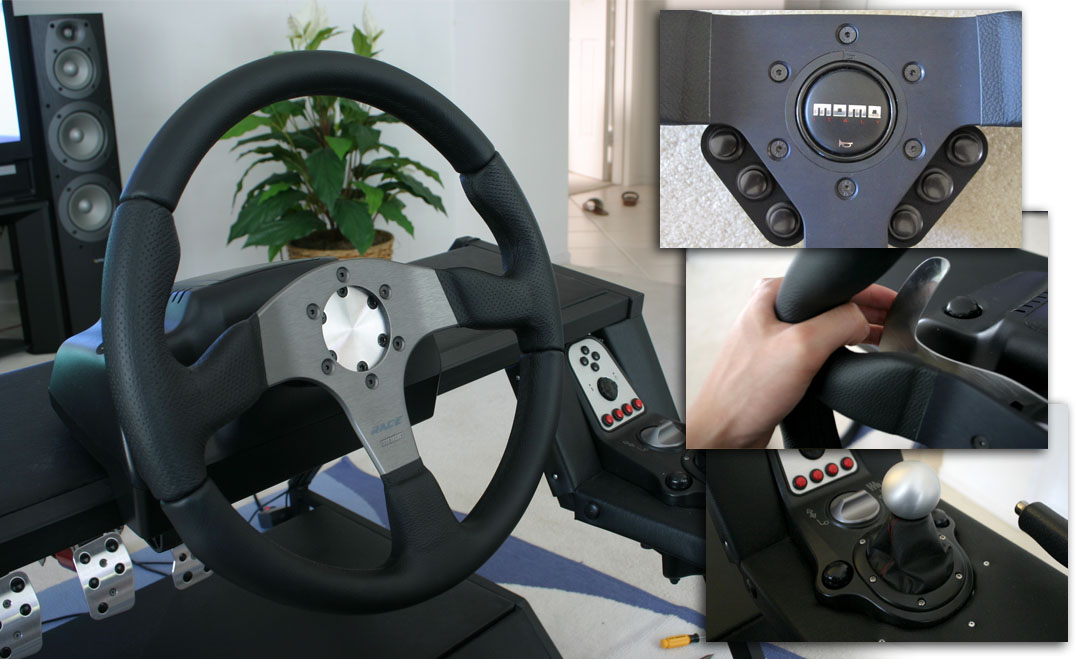
The enthusiastic reception this cockpit received on internet forums and my YouTube channel was overwhelmingly positive, becoming a significant motivator for continued development. Inspired by the community's engagement, I further enhanced the design by creating a range of custom components. These included precision aluminum steering wheel adapters for mounting authentic racing wheels, solid aluminum replacement shift knobs for improved tactile feedback, a bespoke leather shifter boot with red accent stitching for a premium finish, responsive carbon fiber shifter paddles for quicker gear changes, and custom-wired auxiliary button panels for expanded in-game controls, among other ongoing refinements.
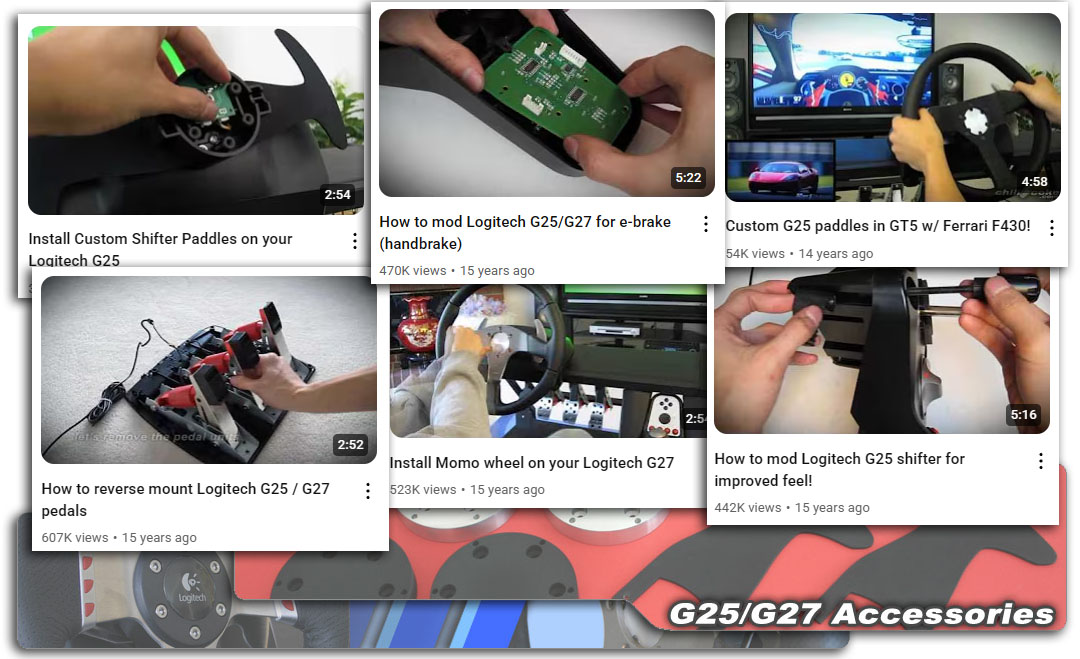
The widespread attention from my cockpit project and its subsequent modifications naturally led to numerous requests for guidance within the passionate sim racing community. Capitalizing on this interest, I began creating instructional YouTube videos, teaching enthusiasts how to perform free or low-cost improvements to their own steering wheels. These tutorials rapidly gained significant popularity, clearly validating a demand for such specialized customizations. Recognizing this emerging opportunity, I launched a business to meet this demand, designing a line of custom components including precision aluminum steering wheel adapters, ergonomic shift knobs, and responsive carbon fiber shifter paddles. Initially, I single-handedly manufactured every component myself before scaling up production by contracting with specialized workshops. Handling the entire fulfillment process, I personally packaged and shipped over 20,000 total units to the community, first via an eBay store and later through my dedicated e-commerce website, chilicoke.com (now archived).
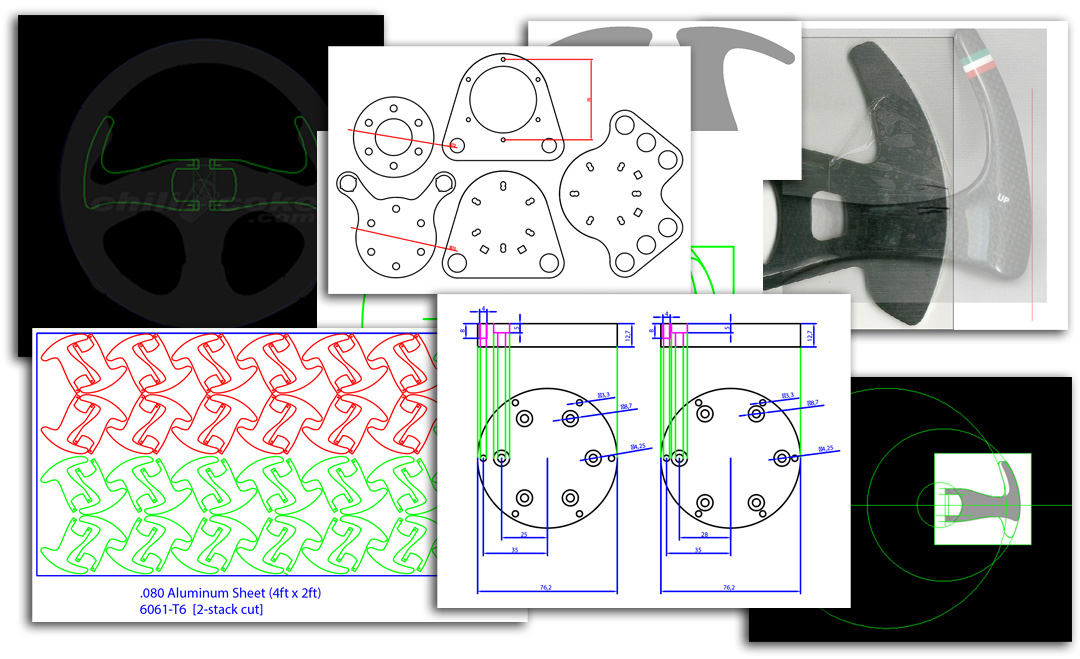
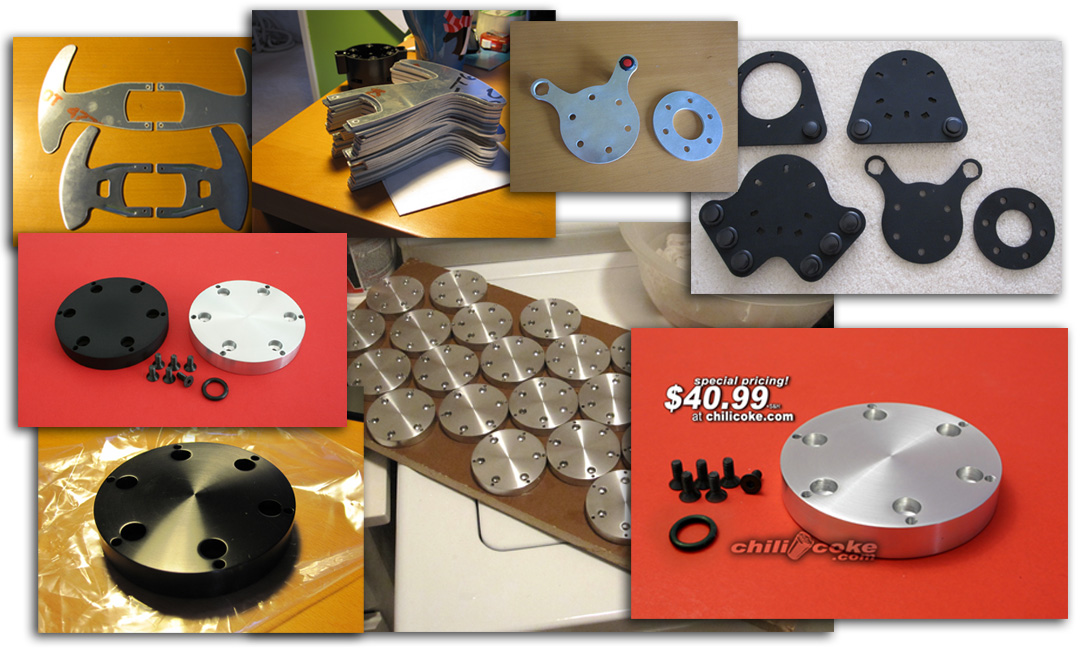
Operating this online venture provided invaluable, real-world experience across the entire product lifecycle. I became proficient in sourcing materials and managing outsourced production, collaborating with various specialized workshops—including machine shops, water jet services, laser cutters, and anodizing facilities. Crucially, this also involved developing skills in direct customer interaction, from initial inquiries and sales to providing ongoing support. Throughout this entrepreneurial period, I remained engaged with the racing simulation community, periodically sharing videos of myself racing on my evolving cockpit, which have collectively amassed over 5.5 million YouTube views to date. Though I've since stepped back from active participation in that community, the project's lasting impact on today's racing simulation is evident. Design principles and features from my influential original build are now reflected not only in many widely adopted cockpit frames, but accessories that I've popularized are now directly incorporated into the controller by the manufacturer.
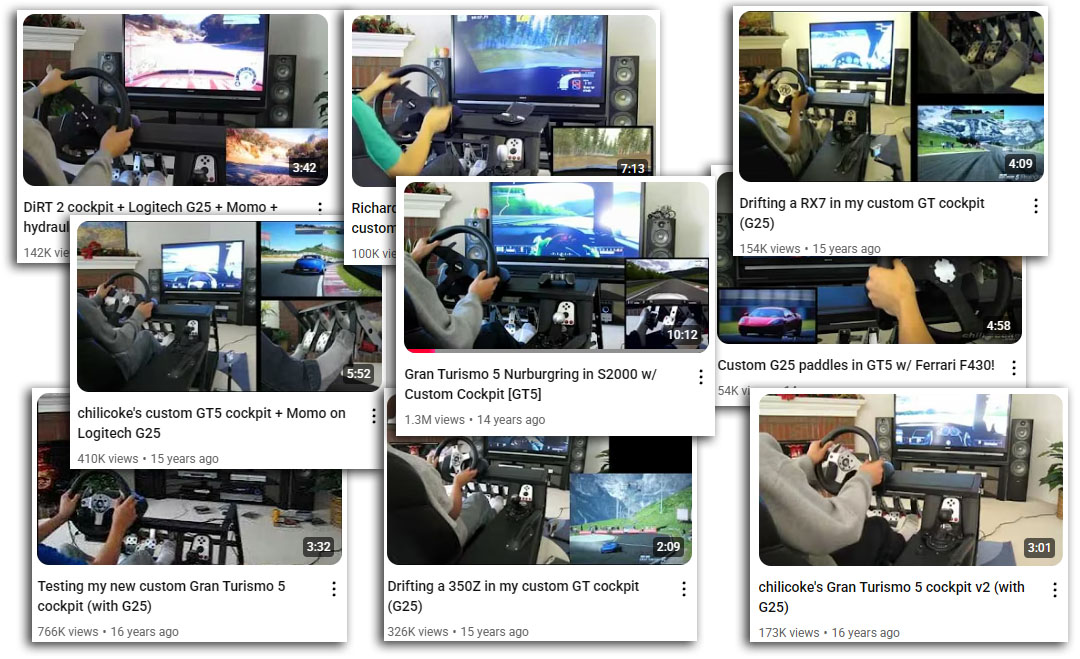